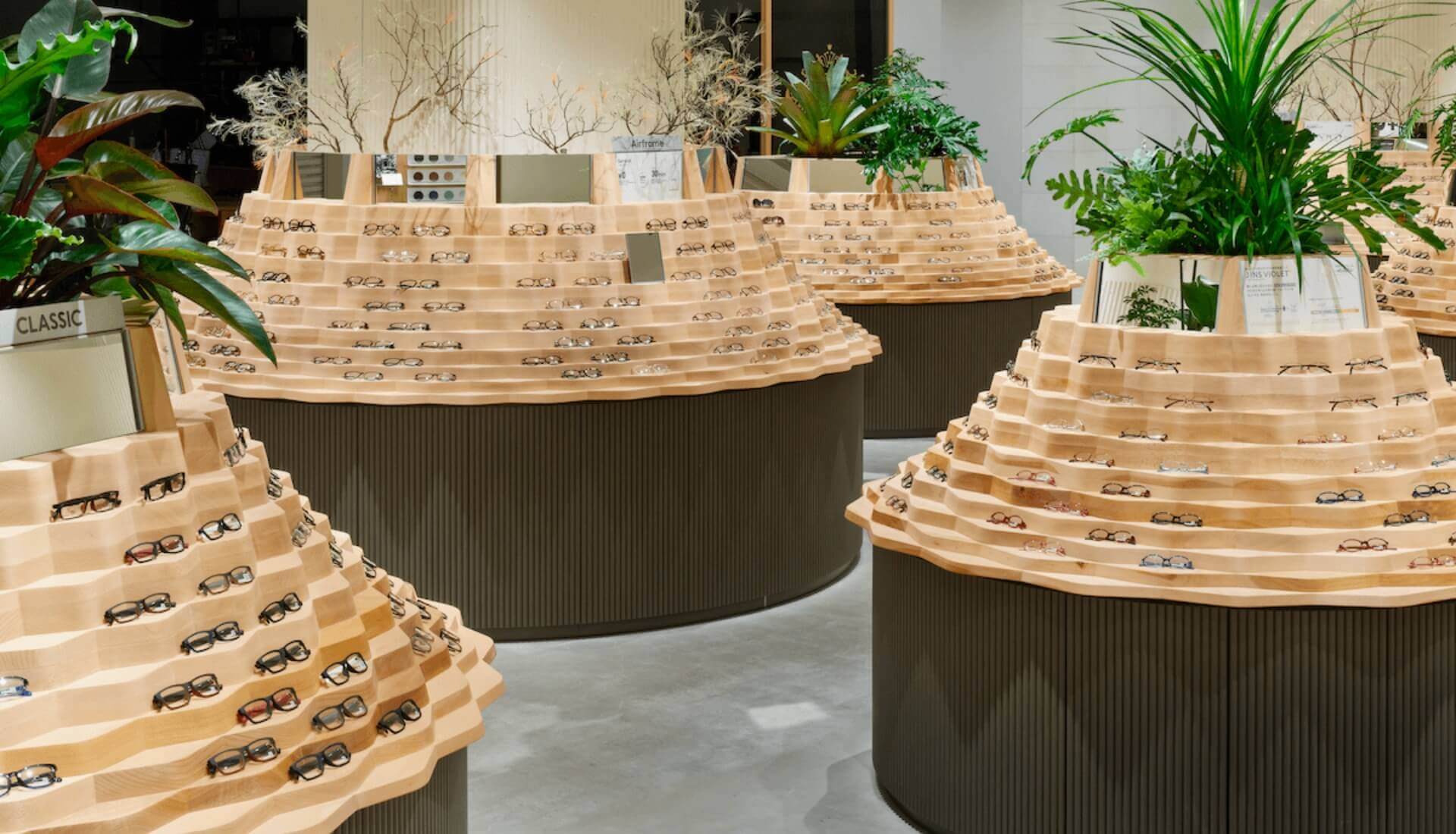
Hidakuma transforms JINS Namba Parks store into an indoor garden with state-of-the-art technology and hardwood
Outline
Collaborating with JINS, one of Japan’s most recognizable eyewear brands, as well as architecture studio KOMPAS, Loftwork and FabCafe Hida’s local timber hub Hidakuma has ventured into the retail space. See how Hidakuma, backed by its extensive expertise in unique custom-made furniture and office spaces, combined technology and traditional craftsmanship to build custom store fixtures with an organic twist.
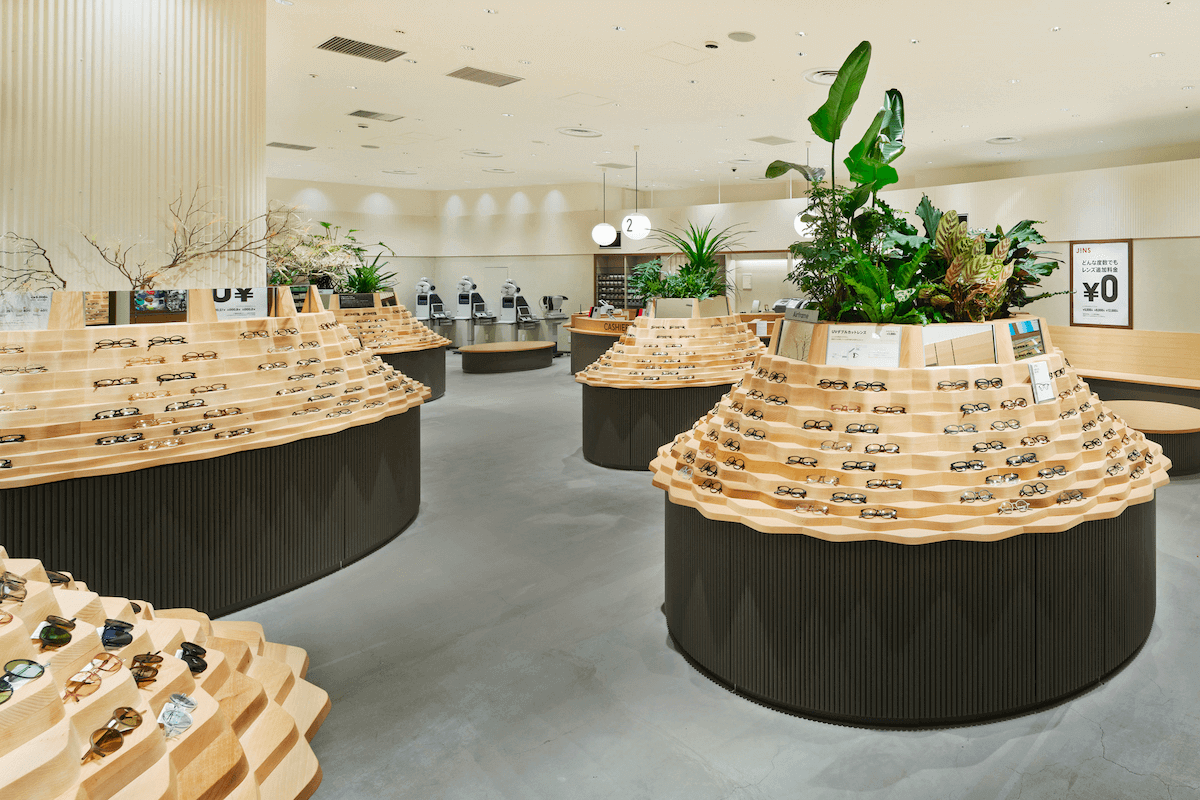
This spring, Japanese eyewear brand JINS opened its JINS Namba Parks store in downtown Osaka. Known for its unique store designs, borne out of creative collaborations with renowned architects and artists, JINS had commissioned architecture studio KOMPAS to take on this premium shopping mall project. Due to the complex production of the store fixtures, Hidakuma – with its unique blend of state-of-the-art technology and traditional craftsmanship – was brought on as a collaborator to help realize the project with CNC-machined wood.
Hidakuma received the 3D data of the fixtures from KOMPAS, which uses designs made from BIM (Building Information Modeling), and redesigned them into a shape that could be programmed with a CNC machine. Hidakuma then proceeded with the fabrication of the seven fixtures, calculating the required number of the hundreds of parts with slightly different shapes for each size and stage according to the parameters, machining time, and budget. Hidakuma supported the project in this short time frame by providing complete direction for the production of the fixtures — from prototyping, selection and procurement of wood, processing and manufacturing, to delivery and installation of the fixtures.
The result is a series of one-of-a-kind circular fixtures that take full advantage of both technology and organic solid hardwoods, to create a unique sense of luxury.
Output
A beautifully grained circular fixture with layered, petal-like tiers
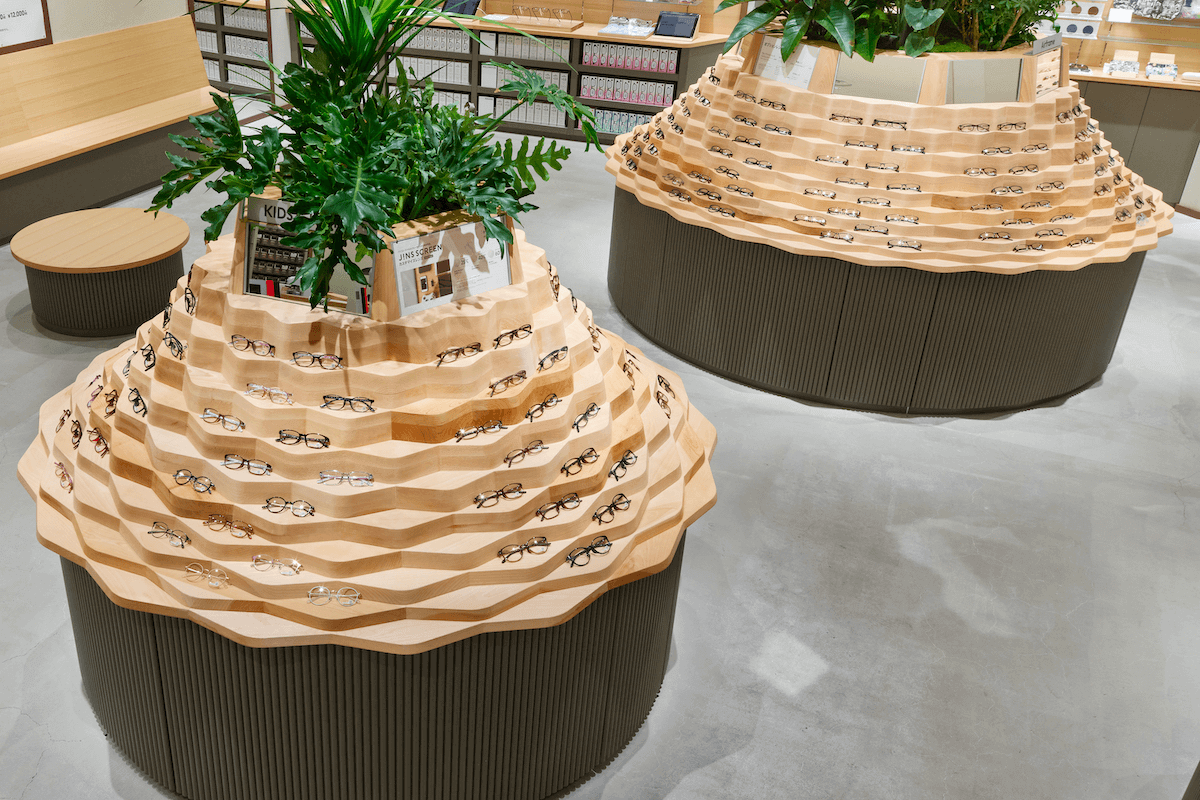
This store interior project was helmed by KOMPAS, led by architect Mai Komuro. Inspired by both the innovative brand of JINS and the lush greenery of the Namba Parks shopping mall, Komuro designed the store fixtures like a landscape, so that each and every eyeglass product would stand out. Unlike conventional rectangular modules, these organic, circular wooden fixtures encourage visitors to move around the store and create a unique presence in the store space.
[Image]
The largest of the seven fixtures, with its tiered stacks, is approximately 1.6 meters high and 3 meters in diameter. Serving as the eyewear display, each wooden part derives from Hida wood. Shaped like flower petals, each compartment is the perfect size for a pair of glasses.
The fixture is made from a mix of seven species of Hida hardwood, seven cubic metres in total. Each tier is of a different height, with a detailed focus on the grain and colour of the planes and cross-sections to create a solid overall impression. The result is a highly textural pine cone-like fixture that invites viewing from different angles, as well as interaction from customers as they pick up a pair of glasses.
Process
Separating 3D modeling, CNC design and fabrication
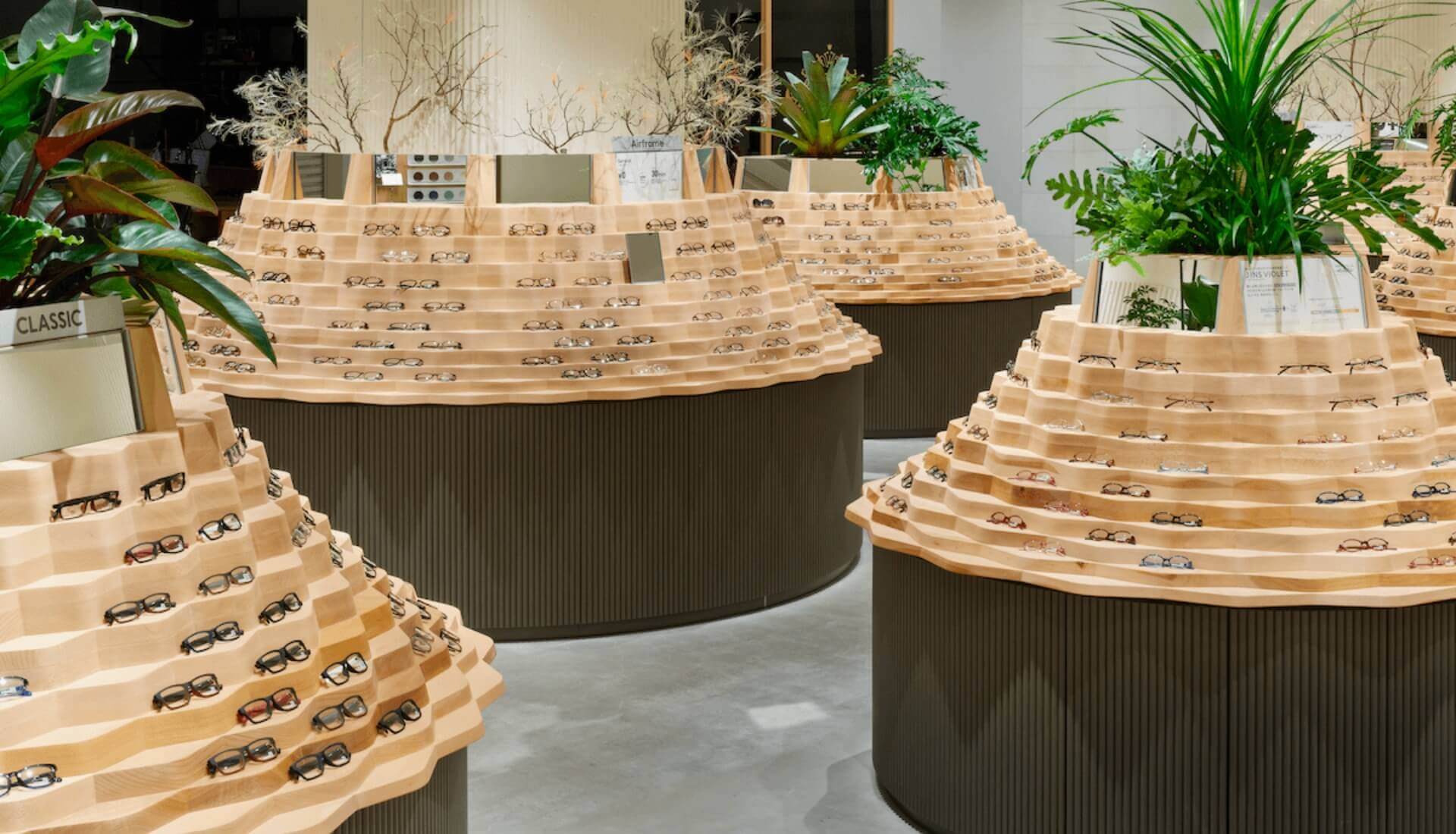
The interior design for this project was first completed by KOMPAS, JINS, and the store construction company. The design of the fixtures was to have the sides of all 11 tiers rise up at an angle, so CNC machining was the main process used.
After consulting with Komuro, Hidakuma converted the KOMPAS blueprints created in BIM into shapes that could be programmed in CNC software. Hundreds of wooden parts had different heights and shapes at each level, and without programming, it was impossible to calculate the machining time and budget for each part.
Prototype check at Hida for wood size and texture
About a month after Hidakuma was consulted, prototype parts were completed. Komuro and a JINS representative visited Hida for confirmation, and Hidakuma was able to share an image of the actual size and texture of the wooden fixtures. The team discussed how the mix of tree species would look, how the glasses would be displayed, and how the fitting mirrors would be installed.
Since they had gone all the way to Hida, Hidakuma also took them on a visit to the local Hida forest, to show them the current state of forestry. Japanese hardwoods are inherently difficult to use because they grow thin and crooked on slopes, but their utilization would lead to the creation of local resource recycling and economic value. The visit also included visiting a log yard and an earthen field where logs are stored after being cut down, as well as a sawmill to see how logs are processed.
Allowing the client and the architect to personally witness every step of the way — from tree growth to product processing — marks one of the advantages of working with Hidakuma.
Utilising leading Japanese CNC machines
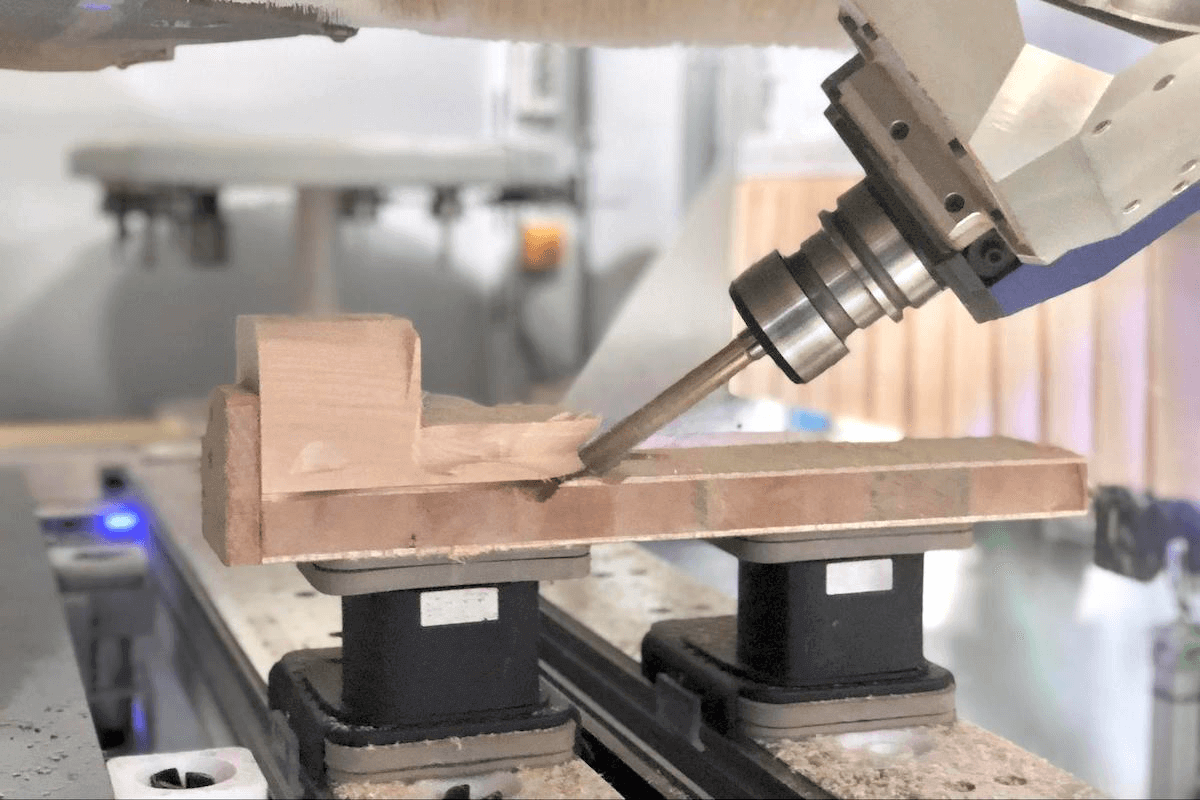
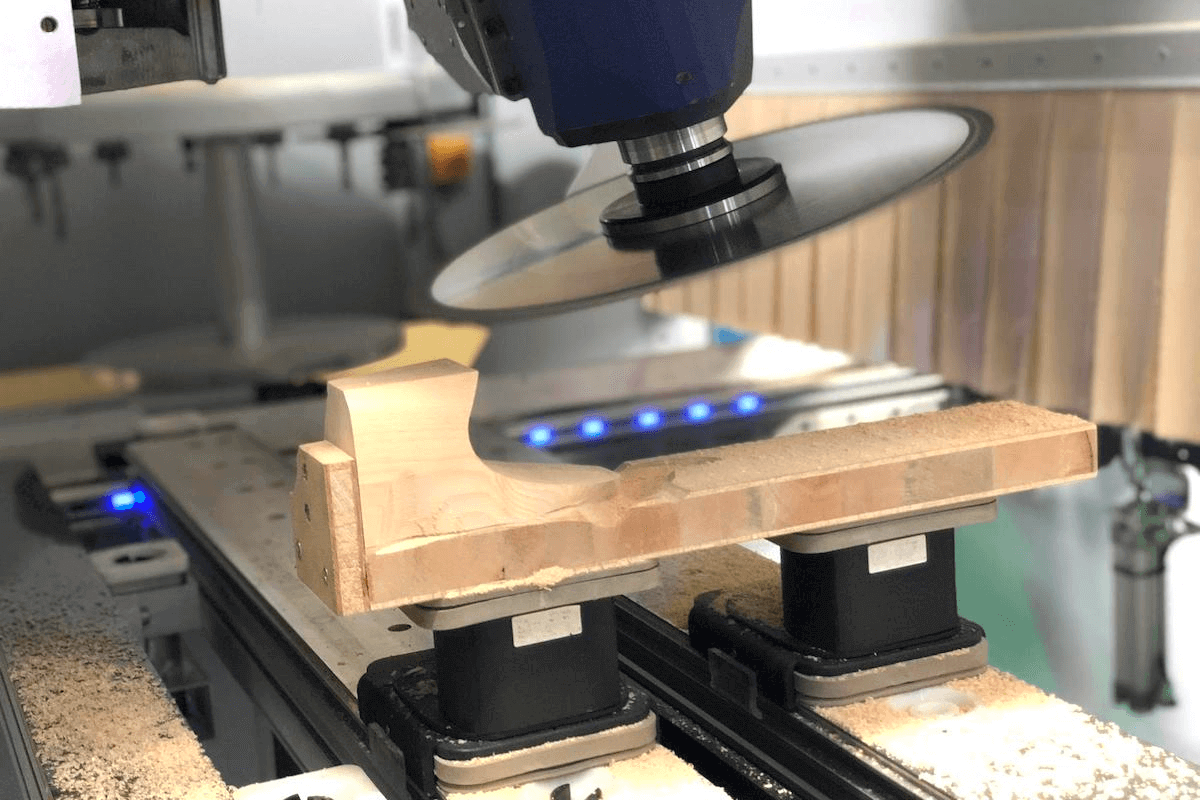
The cutting of the pleated wooden part that prompted the consultation with Hidakuma was a very time-consuming process that would have needed to be done by hand. Hidakuma chose Artistry, a custom furniture manufacturing company in Aichi Prefecture, Japan, as its partner, and utilised their 3D multi-axis CNC machine, one of the largest in Japan, to produce the shape exactly as shown in the drawing.
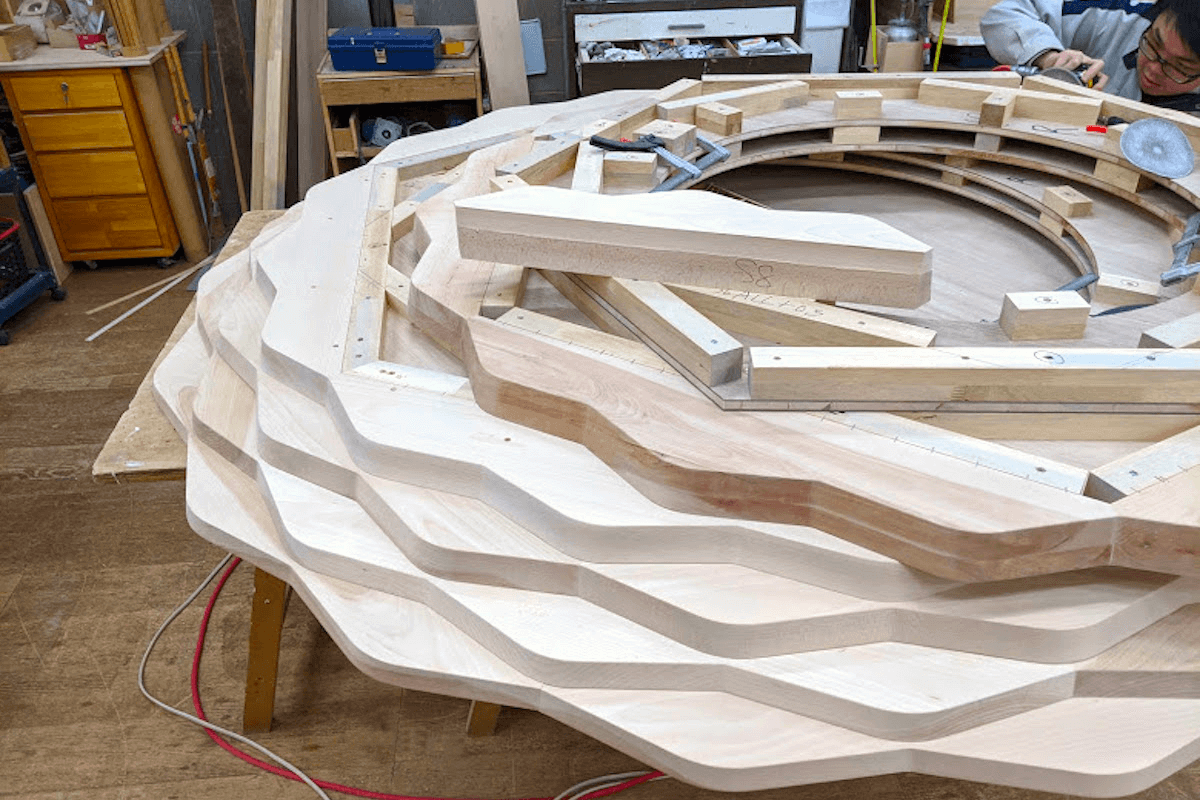
In the production of the upper half of the fixture, which is a complex design, the doughnut-shaped base and folded parts are stacked as one piece. The base is dodecagonal for the XL size fixture, dodecagonal for the L size, octagonal for the M size, and hexagonal for the S size. The outer shape gradually becomes smaller and thicker as the tiers increase.
From Aichi to Osaka, construction work pursued to the last detail

After about a month of fabricating seven fixtures, they were finally brought in and installed in Osaka. Hidakuma and its craftsmen worked together for four days to install the fixtures at night after the store was closed. Because CNC was used to determine the positions for assembly, the assembly part of the process was completed in one day by a team of six craftsmen.
With Hidakuma’s local Hida resources and networks, as well as its technology and knowledge, the company was able to connect architects with the right lumber mill and production partner for this project, providing full support from design to construction.