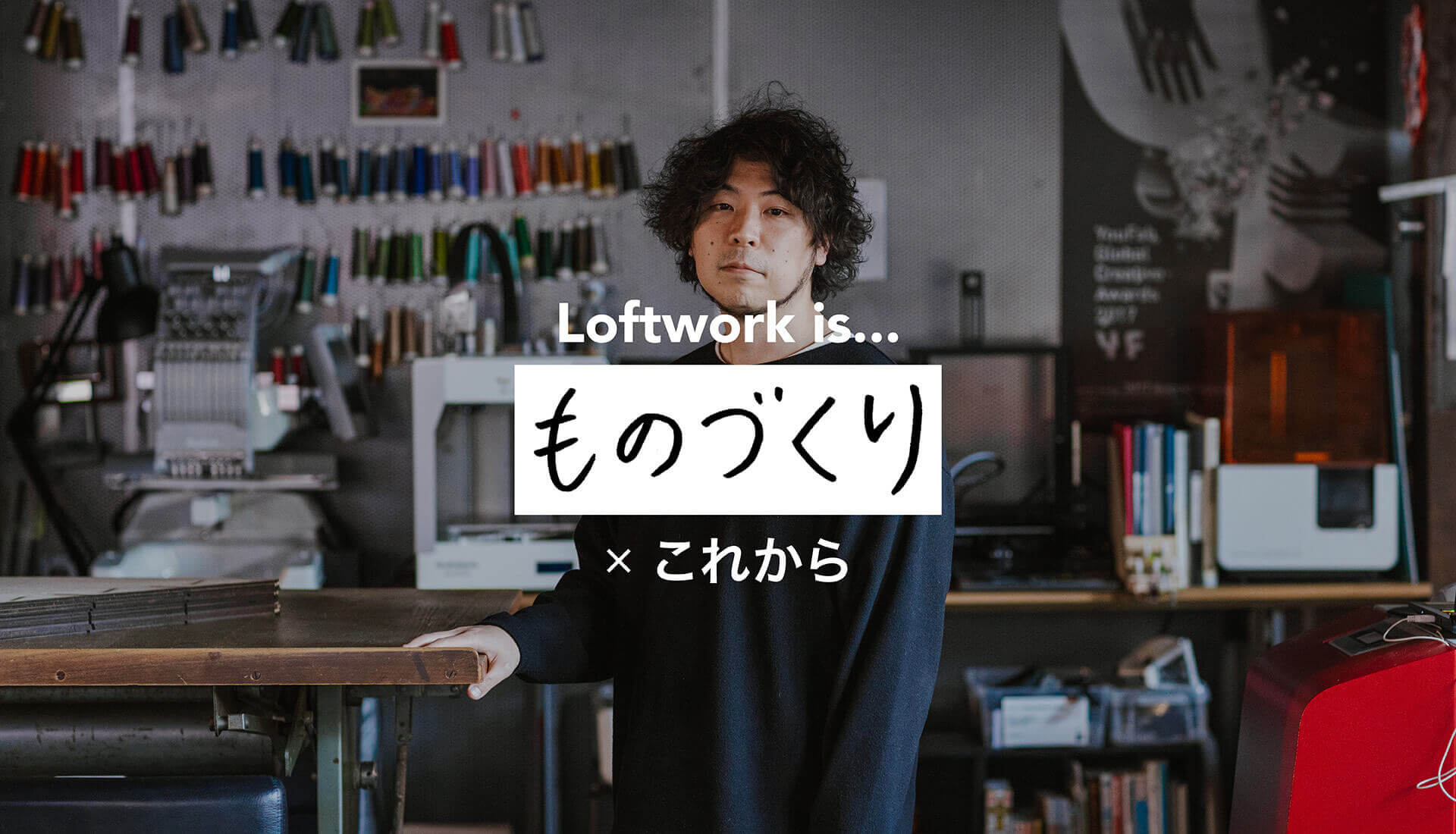
Loftwork is… The future of making.
Creating alternative options within a rigidly structured industry.
A future where creators become instigators, as envisioned by Kosuke Kinoshita
As Loftwork celebrates its 23rd anniversary, it has engaged in projects and businesses in a wide range of fields, from digital creativity to community design, placemaking, innovation creation, and addressing social issues. In the second season of the "Loftwork is..." interview series, we will further highlight Loftwork's "creativity" by focusing on its "people and activities."
Today’s theme is the future of manufacturing.
FabCafes are places where people gather. Equipped with digital manufacturing machines such as 3D printers and laser cutters, these maker hubs serve as the base for creative communities that bring about the innovation of the future.
Managed by Loftwork’s Kyoto branch, FabCafe Kyoto is an experimental space where people involved in manufacturing and material development come together with experts from various backgrounds to innovate the future.
Some of the various activities carried out at FabCafe Kyoto include the operation of MTRL, a platform that supports co-creation and innovation between material manufacturers and creators, and COUNTER POINT, a three-month-long residence program for conducting creative public experimentation.
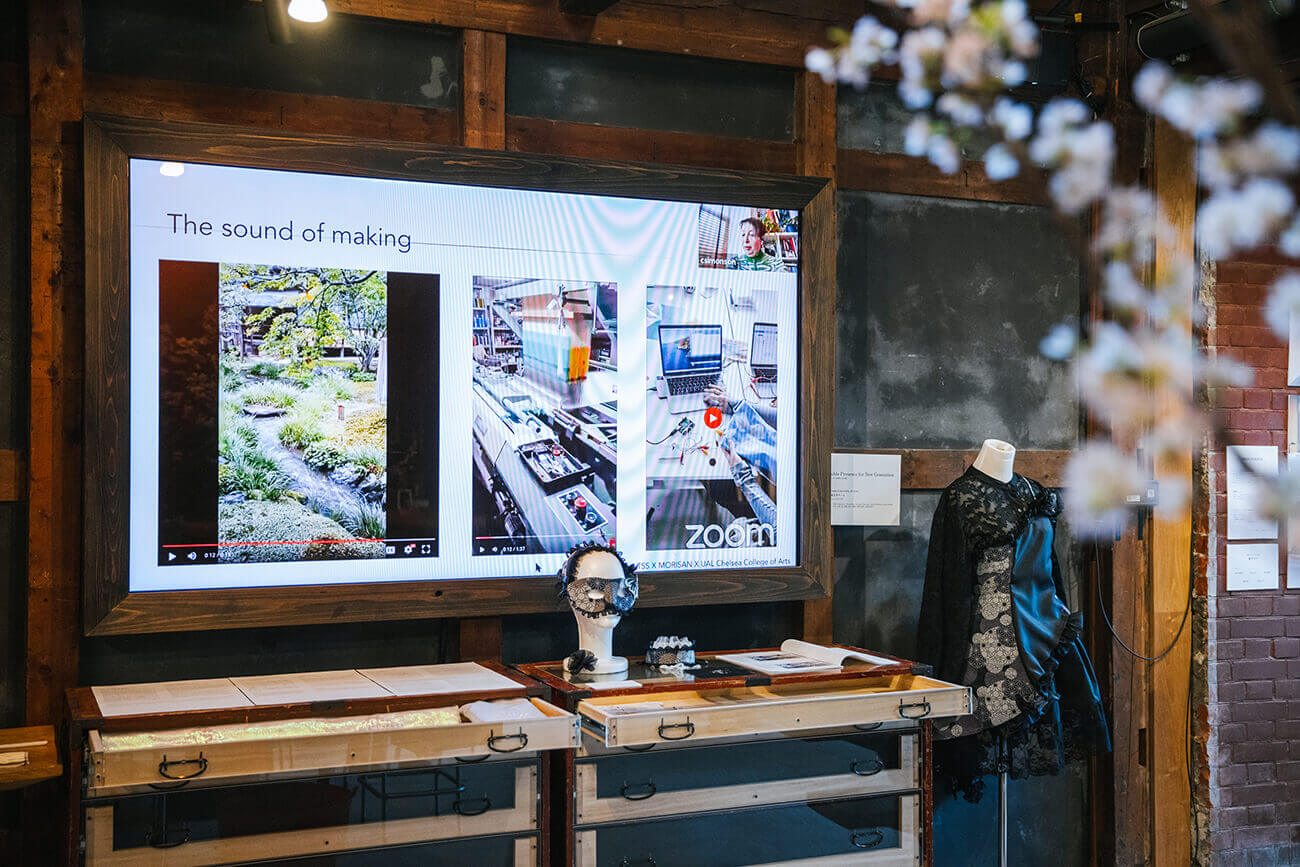
Kosuke Kinoshita, FabCafe Kyoto’s brand manager who plays a major role in the marketing and production areas, uses this space as a launch pad to continually approach those who are engaged in manufacturing and materials development.
Thanks to Kinoshita’s consistent efforts, FabCafe Kyoto has become a place where material developers and manufacturers can connect with people and technologies from different fields, thus initiating various “chemical reactions” (meaning new combinations of personal connections, interests, and knowledge that lead to innovative ideas) and interesting collaborations.
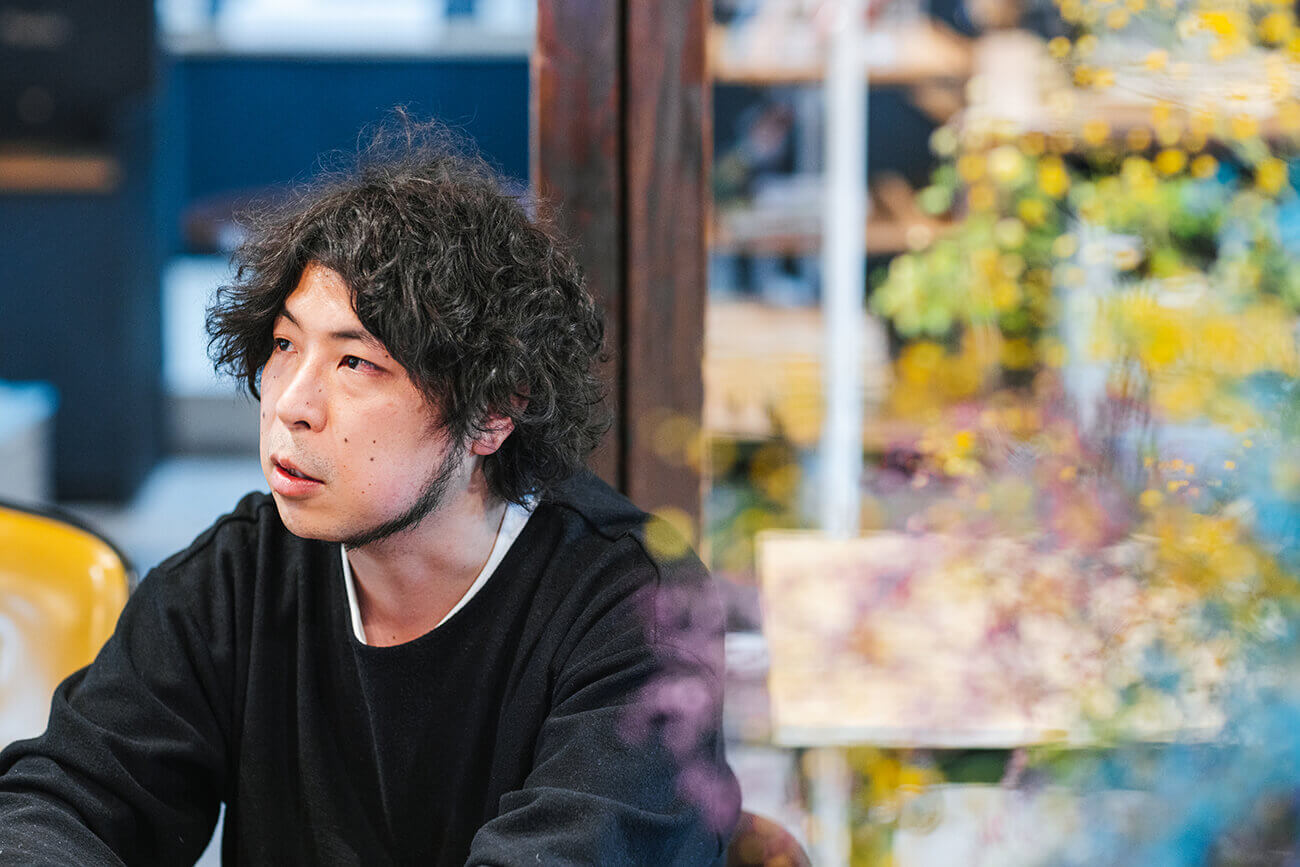
Regardless of industry, “products” are distributed after going through many processes such as materials manufacturing, materials processing, product development and design, inspection, market research, planning and sales.
Leveraging his knowledge of this complex ecosystem, Kinoshita’s thinking focuses on “garnering more respect for creators”, and hopes to “create alternative options” in a manufacturing industry that is rigidly structured.
In this interview, we spoke with Kinoshita—who envisions a future where creators are presented with a variety of choices and where there is equal respect between product manufacturers and users—about the future of manufacturing and materials development.
Interviewing, writing: Miki Osanai
Photography: Yuta Ogura (Akatsuki Shabou)
Planning, interviewing, editing: Quishin
Interview series directed by Ryoko Iwasaki (Loftwork Editorial Department).
The English version has been translated and edited by Sarah Burch and Judit Moreno (Global Editorial Team).
A desire to “break the hierarchy” of manufacturing
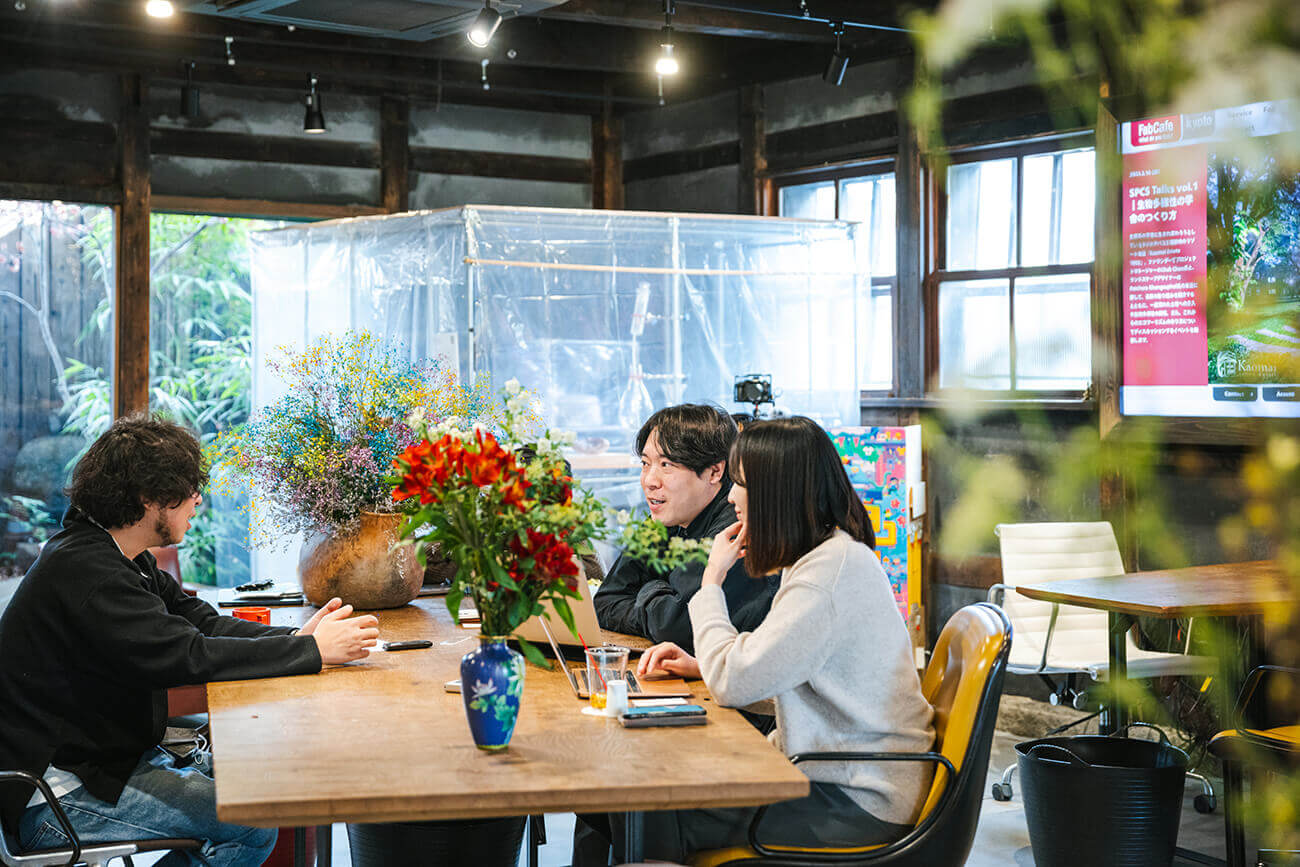
── Looking back on your career, we learned that before you joined Loftwork and became the Fab Director of FabCafe Kyoto, you worked at the IID – Ikejiri Institute of Design. We were wondering if you have any underlying thoughts on your approach to manufacturing?
My fundamental attitude is that regardless of whether they work in manufacturing or not, I want essential workers—who strive to maintain the foundations of society—to be given proper respect for what they do. I want to turn a spotlight on the various people who support our lives to keep them stable.
When applied to the realm of manufacturing, I’m referring, for example, to those who are involved in civil infrastructure or materials manufacturers that produce building materials. I am not capable of manufacturing even a single screw, to be fair, I’ve never even thought about trying to do that—but we can live peaceful lives thanks to the people who produce large quantities of these items with faultless precision. It’s not something we usually stop to think about, but I’m honestly in awe of everything that goes on without us consciously realizing it.
── That’s true. Our lives are built on a foundation of products and things that are made by someone else. Does your desire for respect towards these creators stem from a belief that this currently isn’t the case?
That’s part of it, but if anything, I think it comes from a hope that the structures in manufacturing could be shaped differently.
The creation of a single product is the culmination of several processes, starting with extracting raw substances, processing them into materials, and then, further processing those into secondary materials and the like. Since the “downstream” players—who create the finished products within these processes—have the highest resolution of consumer needs, it’s almost an inevitability that they are the ones standing at the forefront of the supply chain.
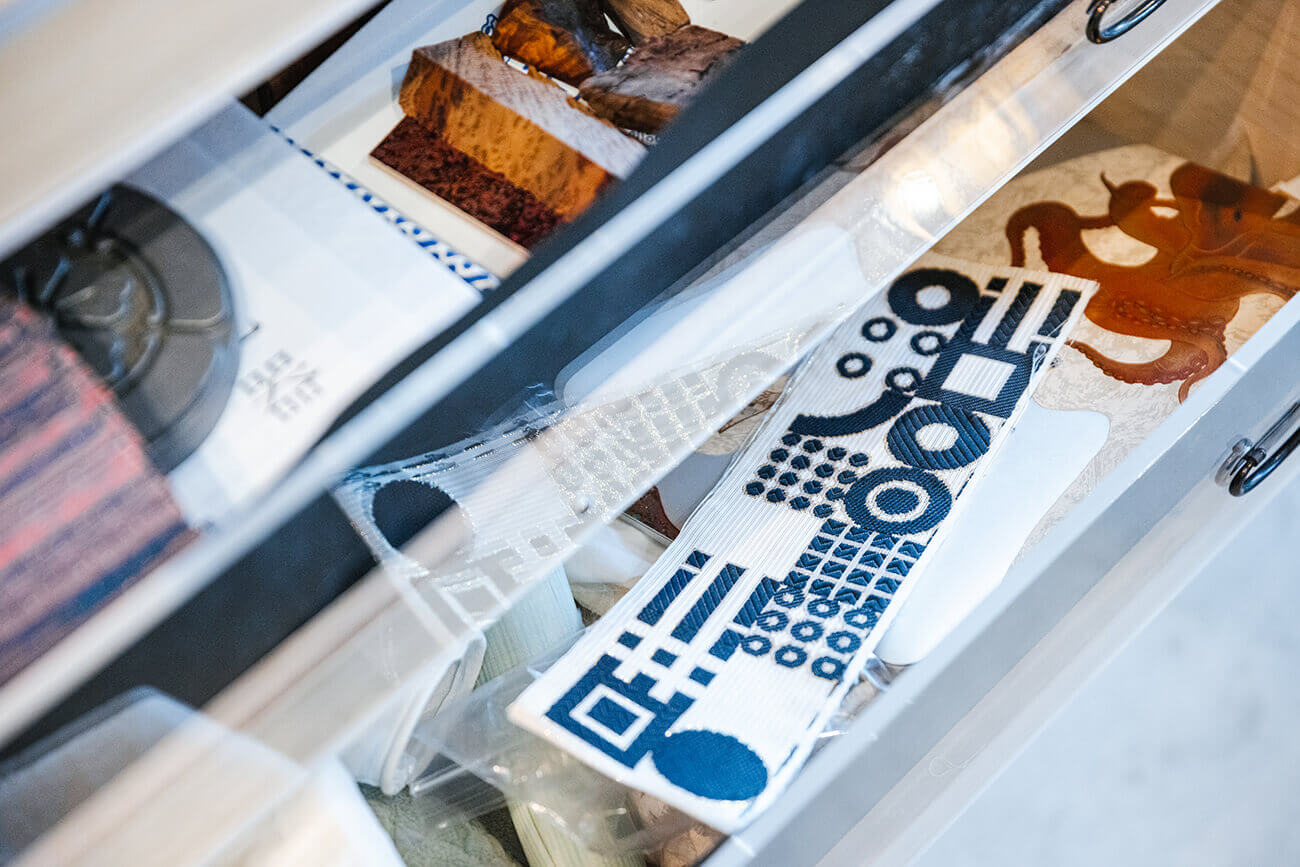
Take the automobile industry for example. In most cases, automobile manufacturers plan products that meet consumer needs. They convey “what they want” to materials manufacturers, who provide them with materials that comply with various complex requirements such as cost and function. Of course, this system has continued for as long as it has because there is a rationale behind it. However, today’s world is moving toward a recycling-oriented society, and I believe there are value propositions that can only be made from the materials manufacturing side.
In a recycling-oriented society, if there is a need to “disassemble a finished product into its original materials for reuse,” materials manufacturers could end up taking the initiative in this disassembly process. If ease of disassembly becomes all the more important for a product’s functionality and experience, technologically savvy and trusted materials manufacturers may become entities that feasibly propose their value to society.
From this perspective, the reorganization of the structure of the manufacturing industry can generate alternative options. At least, that’s my hope. At MTRL and FabCafe Kyoto, we aim to change the order-receipt relationship by reframing it, as well as generating new value by altering the context into something different than it has been until now.
── Where does your inspiration to reorganize the structure of the manufacturing industry come from?
It’s only recently that I was able to put this feeling into words. After going through various events, I realized the current hierarchy was something that had always bothered me.
I can’t point to just one reason, but I would venture to say it’s because I’m a fan of music—especially subcultures and countercultures. I believe that those involved in creative work have a countercultural temperament that resists excessive authority (to varying degrees of course). Maybe that’s the starting point for me.
The shift of values in our society is slowly starting to change various structures. I feel like we are entering a time where businesses can carry on without reliance on “traditional heavy hitters” like capital, power, and influence.
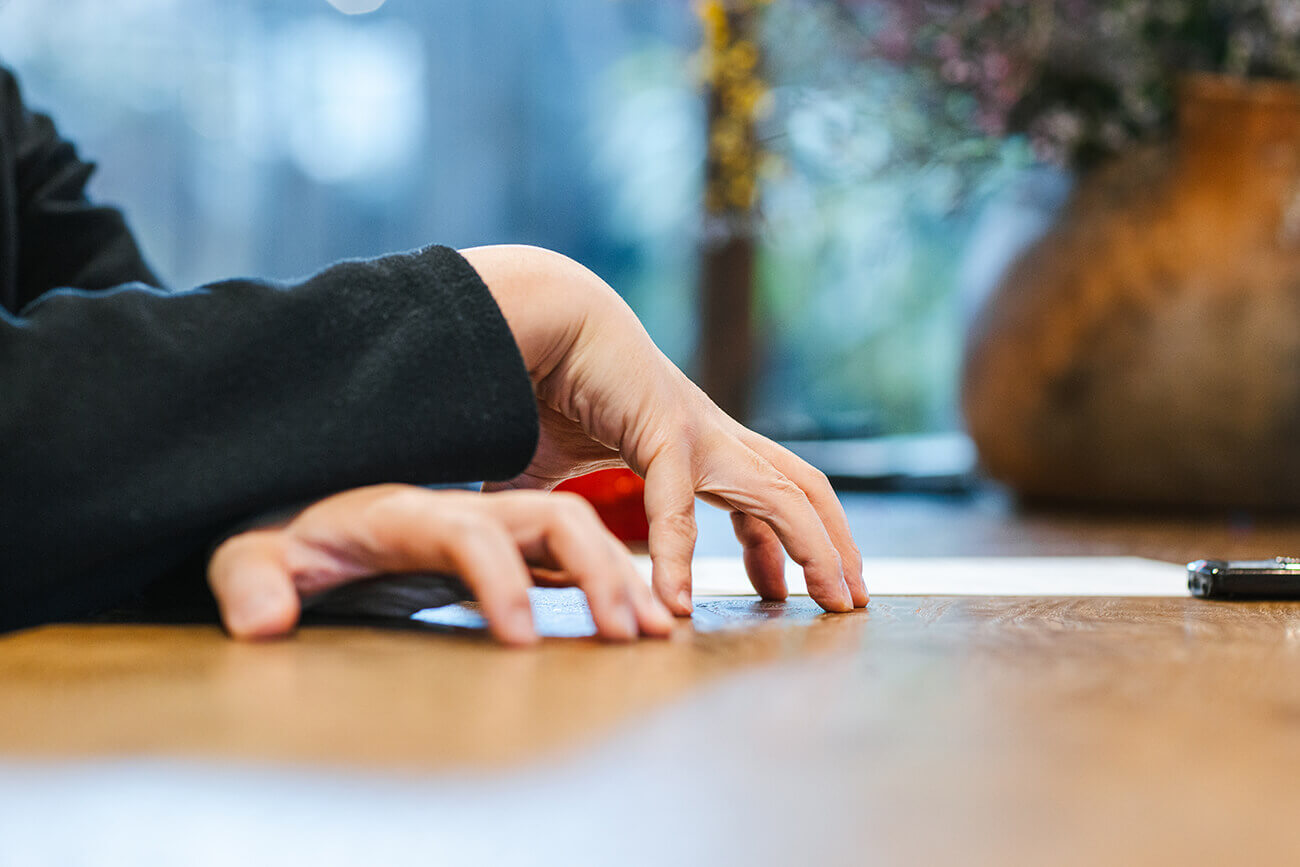
I believe that one of the reasons for these structural changes is the spread of terms such as “circular economy” and “circular design” in business contexts. When they first appeared on the scene, many people felt a vague awareness that they should “be doing something good for the environment,” but now there is a more practical awareness that “it also makes sense economically.”
This leads not only to structural changes in the supply chain, but also to a remapping of stakeholders in the first place. It can even change the way teams are formed. For example, allowing parties A and B—who never had a contact point before—the chance to join forces and achieve amazing things together.
A diagrammatic representation of this can be found in Circular Design: Products, Services, and Businesses for Creating a Sustainable Society, a book co-authored by Daijiro Mizuno and Kazutoshi Tsuda. I feel there is great potential to design the supply chain of the future when people from different fields come together to collaborate in new ways.
Initiating chemical reactions that unlock the potential of creators
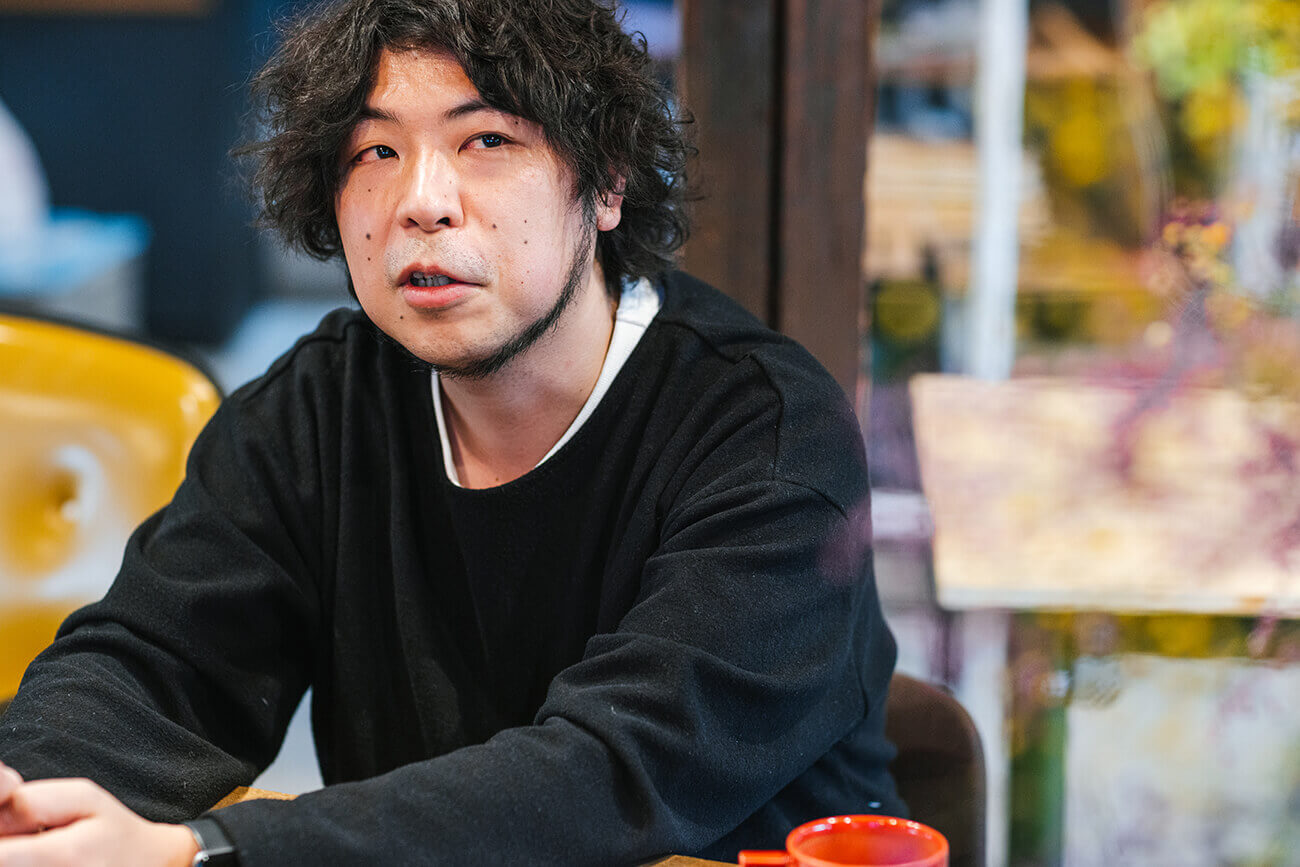
── You hope for the generation of alternative options through initiatives on the side of the materials manufacturers, and collaborations between people from different fields. What will come from these new elements?
I believe it is easier for more chemical reactions to occur among people when changing the order-receipt relationship within the manufacturing framework, or when creating contexts for experts from different fields to work with each other.
── So, chemical reactions happen as a result of increasing the range of choices?
That’s what I believe. It’s the reason why I’ve continued to connect people to people, people to technologies, and people to places that aren’t adjacent to them. Before joining Loftwork and FabCafe I worked at the IID – Ikejiri Institute of Design, and before that, at galleries and cafes that featured contemporary art. But regardless of the position, I have always tried to act as “a connecting agent.”
── A connecting agent?
Strictly speaking, it’s not like I’ve been involved in making matches that seek conventional success as a product. Rather, I focus on designing and implementing one-time chance encounters. It is a step way before the materialization of a product, but it is important because it is the moment when we need the wildest freedom and imagination to allow for the unexpected to happen.
People don’t often realize just how differently experts of varied fields use the same technologies and materials. With that premise in mind, FabCafe Kyoto started to host the Fab Meetup Kyoto once a month as an event where participants from diverse backgrounds can gather and share projects and ideas related to different creative processes.
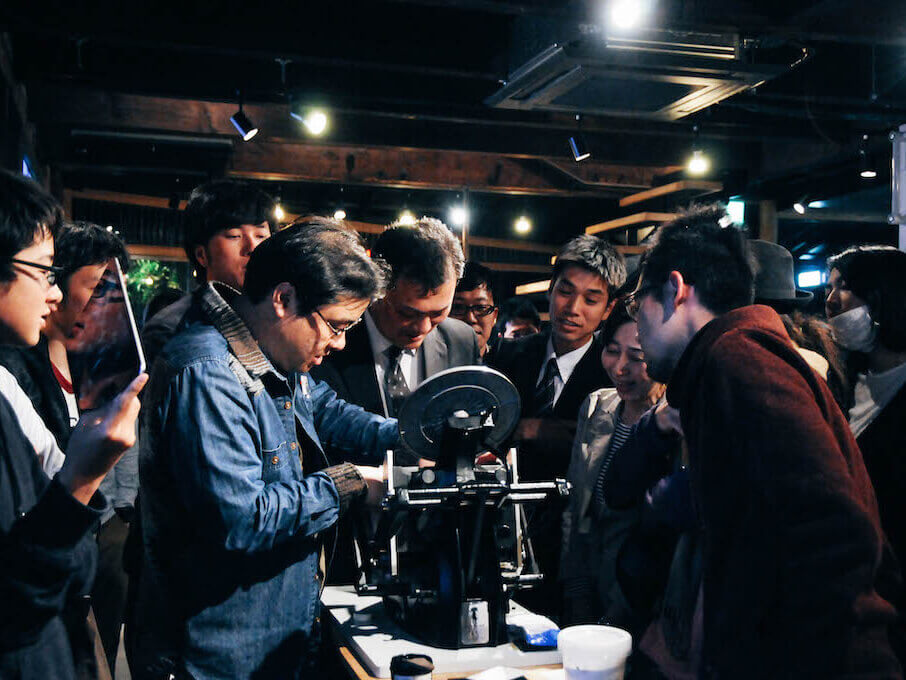
Once the pandemic began to settle down, a university professor who often attends these events told me, “This is a place where you have a high probability of encountering interesting information that you wouldn’t be able to find just by looking it up yourself.” This is what happens when a group of people from various backgrounds come together under the common language of “making.” In a digital age when anyone can quickly obtain whatever knowledge they seek, his words reminded me that the world needs places where people can find information unavailable through conventional search methods.
── You have mentioned that you are not usually involved in making matches that seek conventional success as a product. What exactly is the aim of these connections and chemical reactions?
Indeed, the goal of manufacturing company collaborations is usually seen as matching them with a designer and creating new products. However, I don’t believe that successful chemical reactions need to culminate in the output of a product.
For example, one of FabCafe Kyoto’s initiatives is the creative residence program COUNTER POINT, which encourages the expansion of individual curiosity and creativity. It’s a system through which participants can use FabCafe Kyoto to conduct public experiments for the limited time of three months.
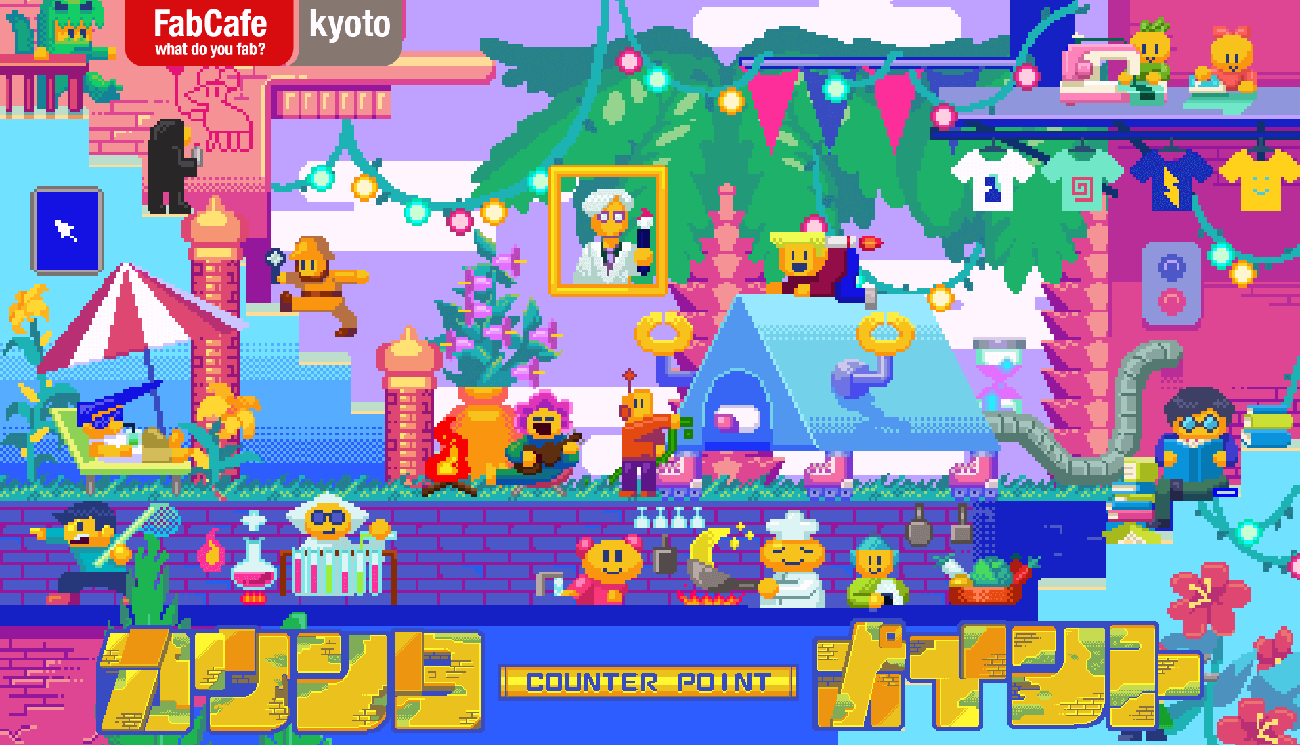
One of the previous participants in COUNTER POINT was an artist who usually works in printmaking. However, during her residency, she used a digital embroidery machine, saying “If I’m going to make something here, I want it to be with technology I’ve never tried before.” As a result, she produced an incredible number of pieces that sold at a tremendous rate at her exhibition.
She said, “In my twenty years as an artist, I thought I’d done it all, but now I’ve found a completely different approach,” which left a really strong impression on me.
When an artist obtains new creation methods and produces completely different outputs, they create new value that can bring people even more happiness. Those are the kinds of chemical reactions that I am seeking to produce, and I believe FabCafe Kyoto’s role is to continue to act as a testing ground where those chemical reactions can occur.
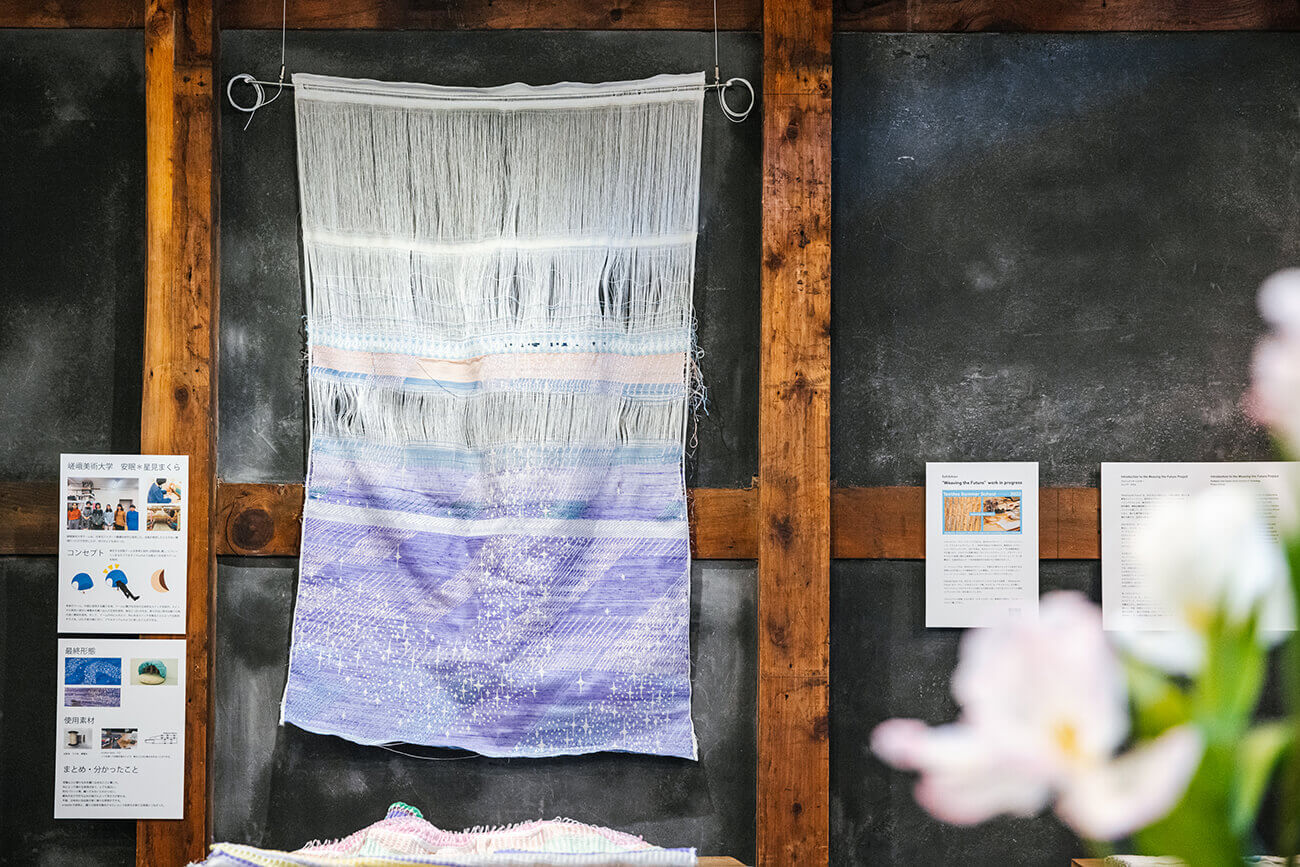
── Information on manufacturing technologies and materials seems to have a rather closed-off image. On the other hand, both you and FabCafe Kyoto are proactively sharing this information. Perhaps that is why it is leading to so many fresh connections.
A common phrase among the Kyoto members about two years ago was “unlocking potential.” It was a way for us to confirm among each other that this was one of the basic attitudes we all held. I think that phrase relates to the concept of opening up something that was previously closed, and maybe it was something our team always wanted to do.
I do not consider myself to be naturally good at widely disseminating information or amplifying value. Still, I often find myself thinking, “How can we make hidden technologies and the possibilities of materials interesting to those in other fields?” That’s what I keep trying to achieve.
Creating a “resilient society,” not through increasing population but by expanding the range of activities
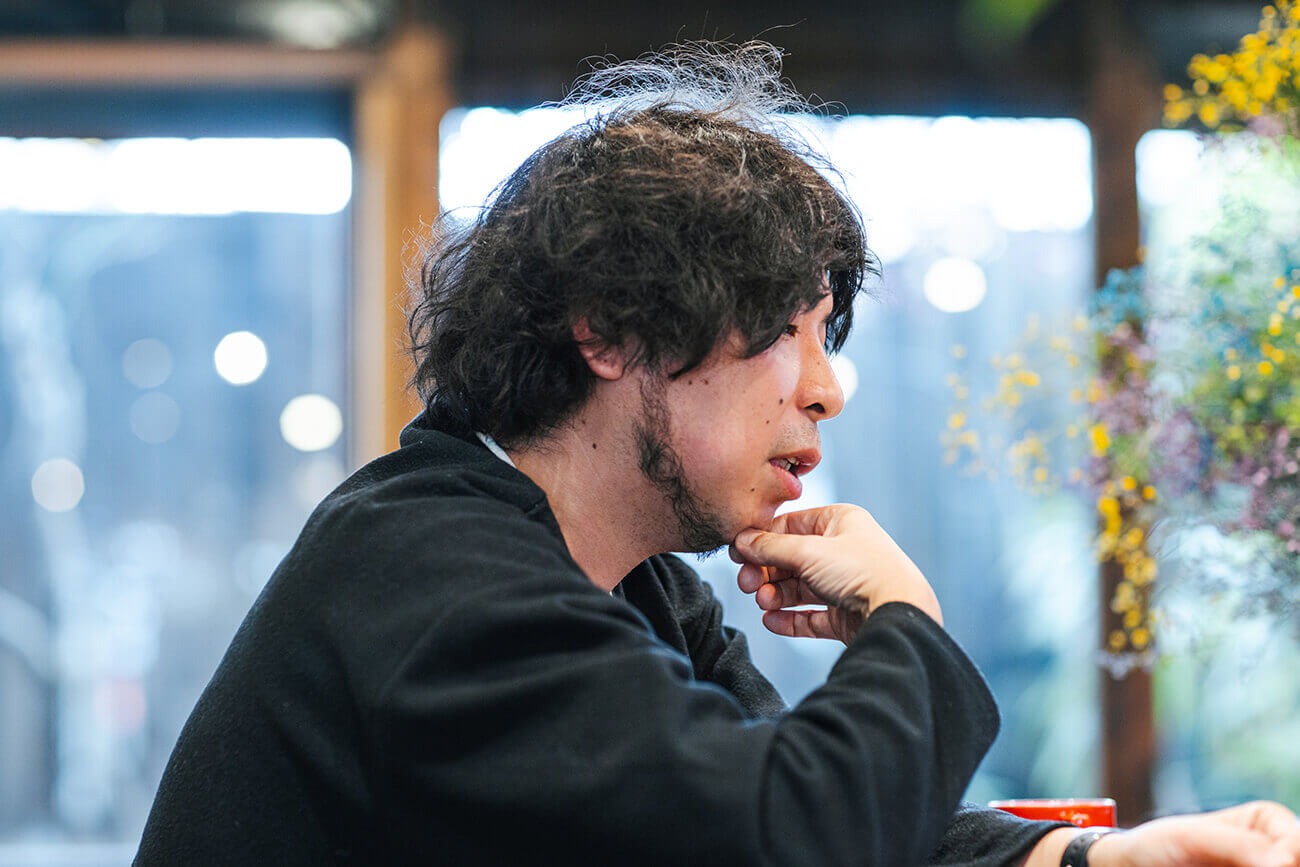
── Going back to your hypothesis that structural changes are taking place in manufacturing, what other aspects do you think will promote significant change besides the recycling-oriented mindset that you mentioned earlier?
The structure of the supply chain is currently experiencing important swifts.
The background for this is, of course, the expansion of circular economies that aim for economic growth while considering the environment. Other factors leading to structural changes are the diversification of tastes and preferences and the fact that “high-mix low-volume” production has become technologically feasible.
Moreover, I believe my role is to bring about further changes to the existing structures by lighting a fire under professionals who have always “manufactured as they’ve been told to” up until now. I’m confident the world will become a more exciting place if materials manufacturers team up with other players to attempt new challenges.
── As I recall, you also mentioned wanted to spark chemical reactions by placing together people or places that weren’t adjacent. Ideally, what would be the result?
The acclaimed avant-garde painter Taro Okamoto once said that he wanted people to react to his works with shocked expressions like, “What in the world is this?!” rather than just a bland “Oh, this is nice”. Now, I am aware that what I’m doing is nowhere near his level, but I’m aiming for the same sort of response.
On a personal level, I love the thought of more weird or wonderful things happening in the world. In the grand scheme, I believe that having many strange things around means we are closing in on a society with greater diversity.
I interpret a society with greater diversity as one where people from all walks of life can experience greater resilience.
In the future, I hope that the system will become one where people who wish to make strange or niche products do not have to pander to economic rationality in order to sustain themselves.
── As you just said, up until now even those who want to venture into creating niche products have to pander to economic rationality. What sort of changes does manufacturing need in the future to break through these barriers?
I think it is important to increase the number of options and expand the range of activities in which materials can play an active role.
Rather than increasing people in manufacturing, it is a matter of an increased range of choices. In the future, I believe that rather than singular approaches, people will utilize multiple options that lead to them attempting things previously considered illogical or impossible. I hope that will take us one step closer to becoming a comfortable society to live in for people from many different walks of life.
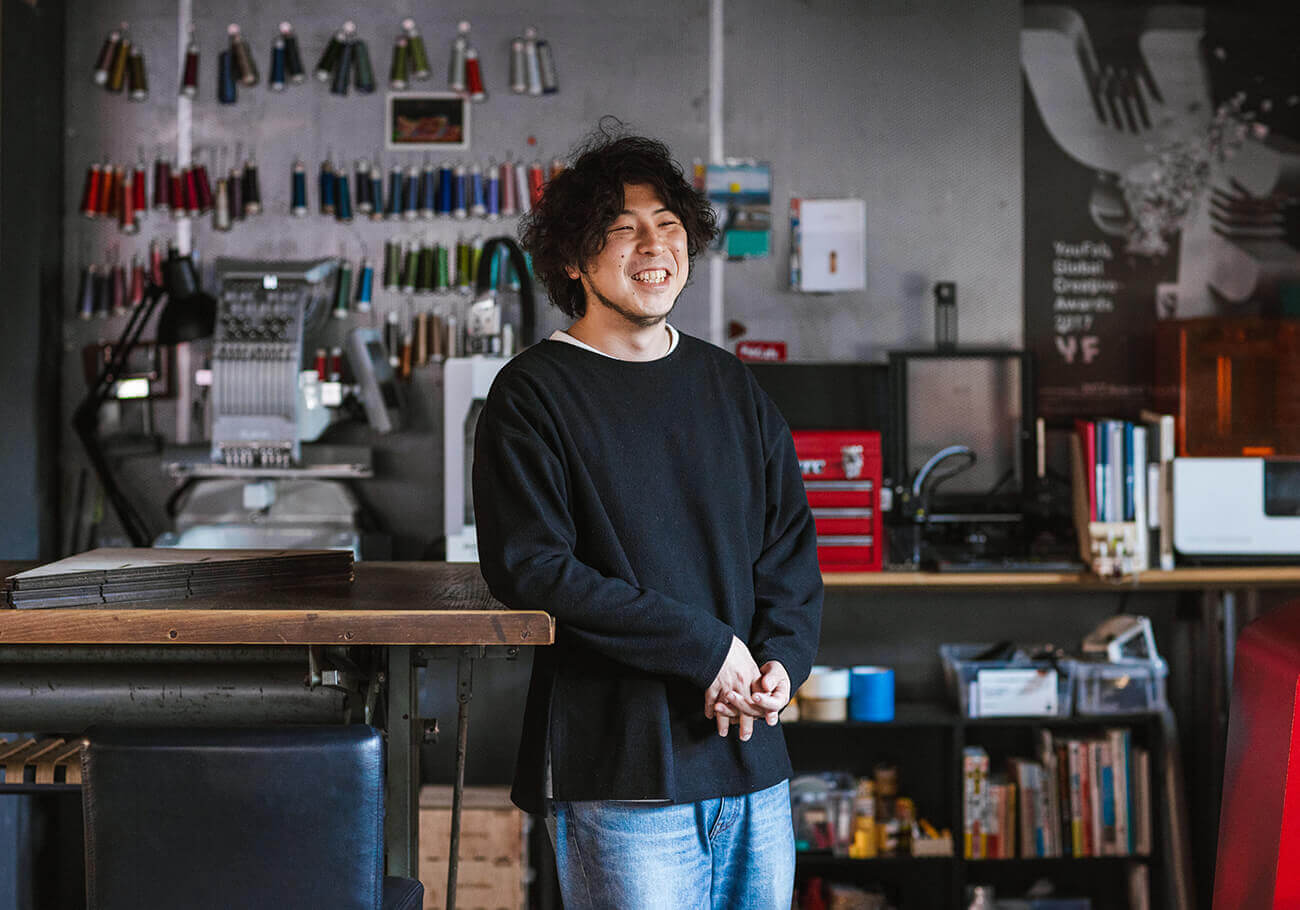
In conclusion
Through our discussion with Kinoshita, we learned that the manufacturing structures are going through a transformative phase.
The diversification of standard and conventional approaches will in turn enrich methods of expression and their provided value.
In the words of Kinoshita, “In our current society, where people all over the world are strive to manifest diverse lifestyles, manufacturing—fundamental to shaping such environments—will increasingly grow in significance.”
To engage as torchbearers in a society where value transformation is rapidly accelerating, individuals, whether directly involved in manufacturing or not, must adopt a mindset of challenging conventional approaches, and take action to expand their horizons by igniting internal chemical reactions.
>>Other interviews in this series (in Japanese)
Next Contents