テクニカルディレクター、Fabの山に登る。~ 諏訪ミニ四駆編 ~
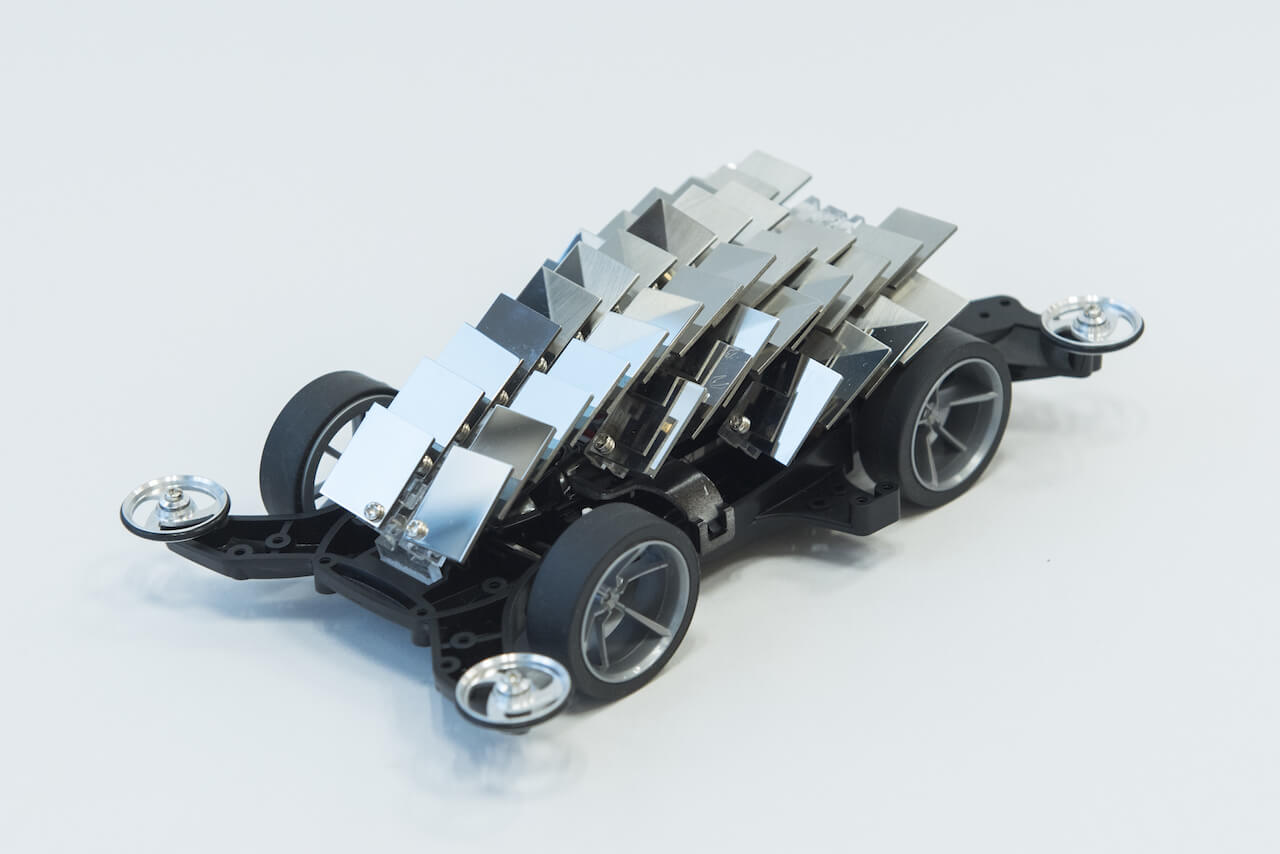
こんにちは。TD(テクニカルディレクター)の藤田です。
昨年8月〜10月の話になりますが、SUWACKATHONというミニ四駆とFab、諏訪の工業技術をコラボレーションしてミニ四駆を作るイベントに参加者として参加し、制作過程の中で学ぶことがいろいろあったので制作過程を記事にしようと思います。SUWACKATHONについて、詳しくはこちらの記事をご覧ください。
諏訪市が世界に誇る精密加工技術の魅力を発見し発信する
http://www.loftwork.jp/column/2017/20171127_suwackathon.aspx
私は運営側ではなくクリエーターとして参加し、恐れ多くもチームで賞を2つ受賞しました!とロフトワークの私が言うと、「え?なんか裏があるんじゃないの?」って思われそうですが、受賞後に審査員の方から「え!ロフトワークの方なんですか?」と言われたほどガチンコです!
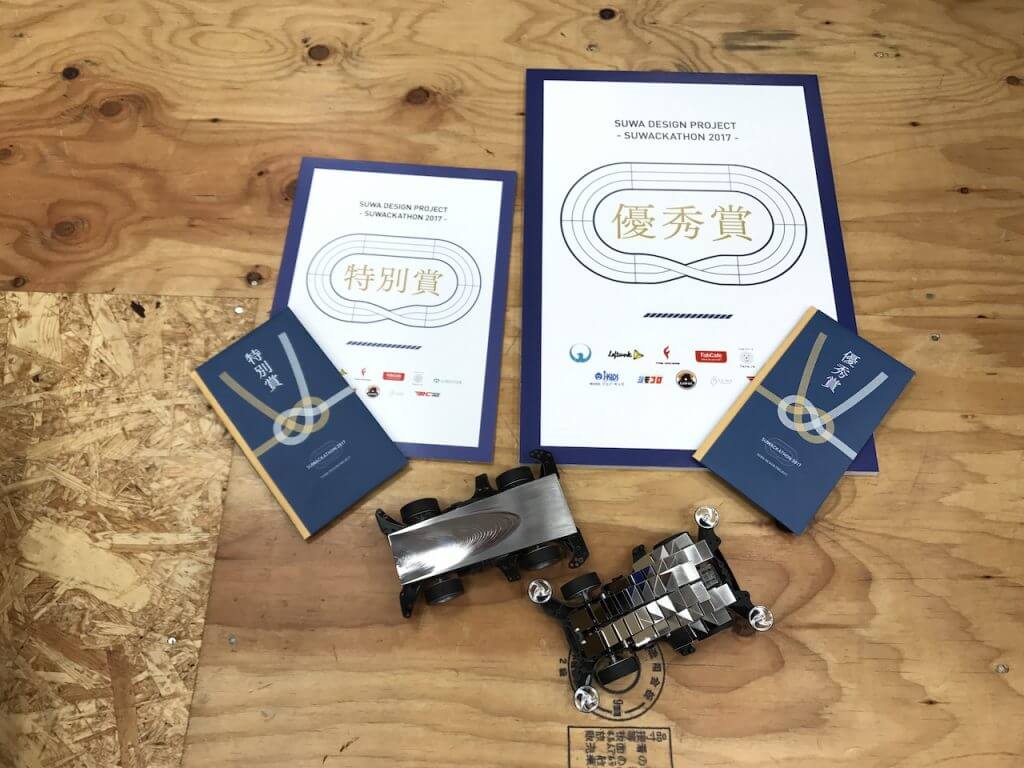
完成したミニ四駆はそれぞれ、刀匠にしか流通しない幻の玉鋼を贅沢にもボディ全体に使った「剣刃虎(ケンシコ)」、鱗のような細かい金属パーツに様々な磨き加工を施した「龍鱗(リュウリン)」。「速そうに見える」ミニ四駆をテーマに、見た目重視で制作したのですが、「技術の凄さがよく伝わる」と評価いただきました。この記事では、私が担当した「龍鱗(リュウリン)」の制作過程についてレポートします。
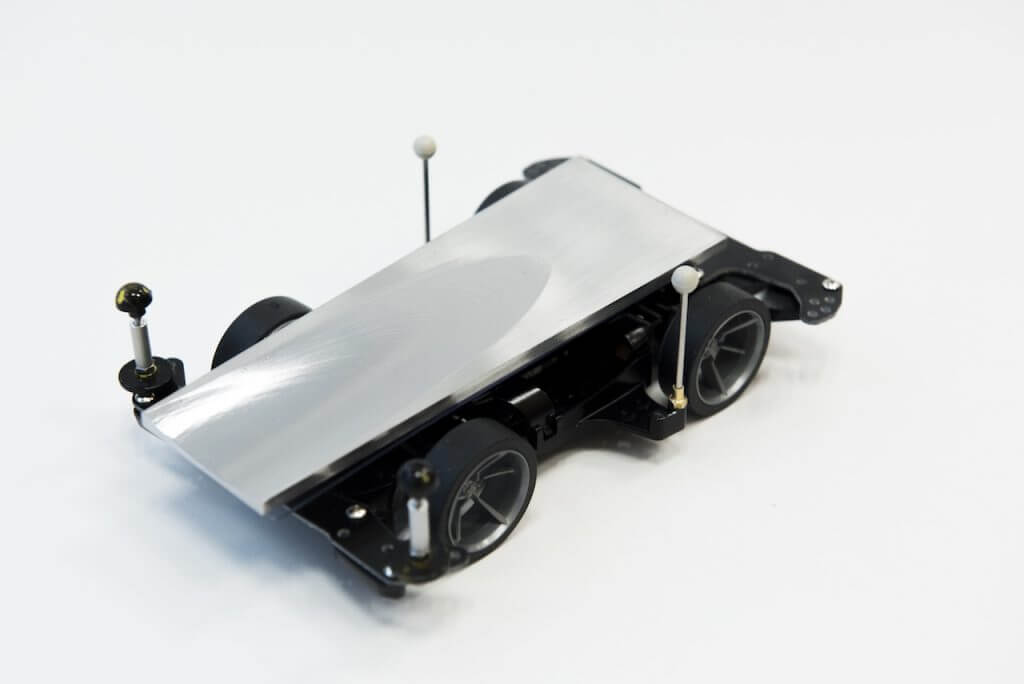
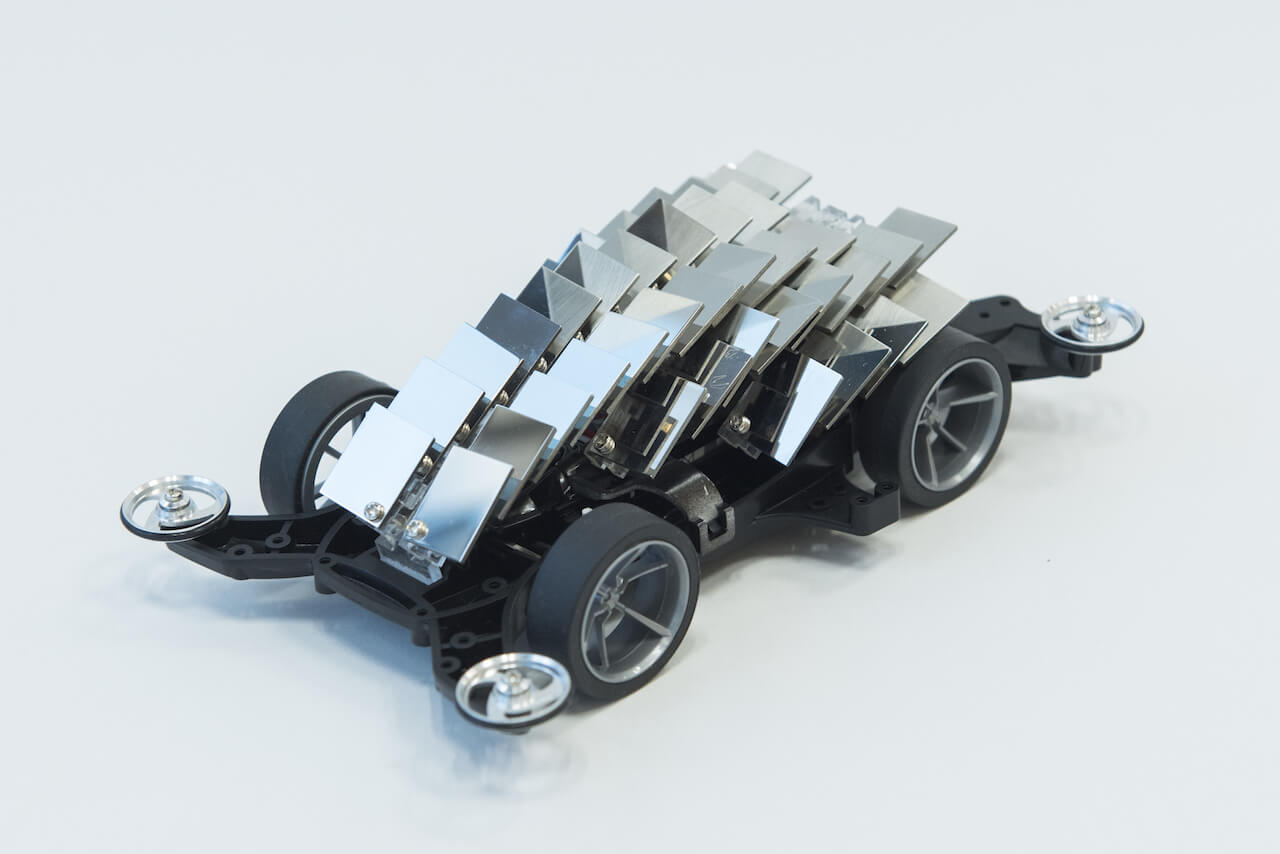
私達のチームは、建築士/イラストレーターの佐藤、システムエンジニアの船倉、テクニカルディレクターの私、というクリエーター3名、いずれもほぼミニ四駆スキル0(汗)。ご協力いただいたのは、精密研磨/切削を得意とする株式会社松一の松澤社長、奥様の松澤専務、玉鋼を提供してくださった足立さん、そんな6名でミニ四駆に挑みました。
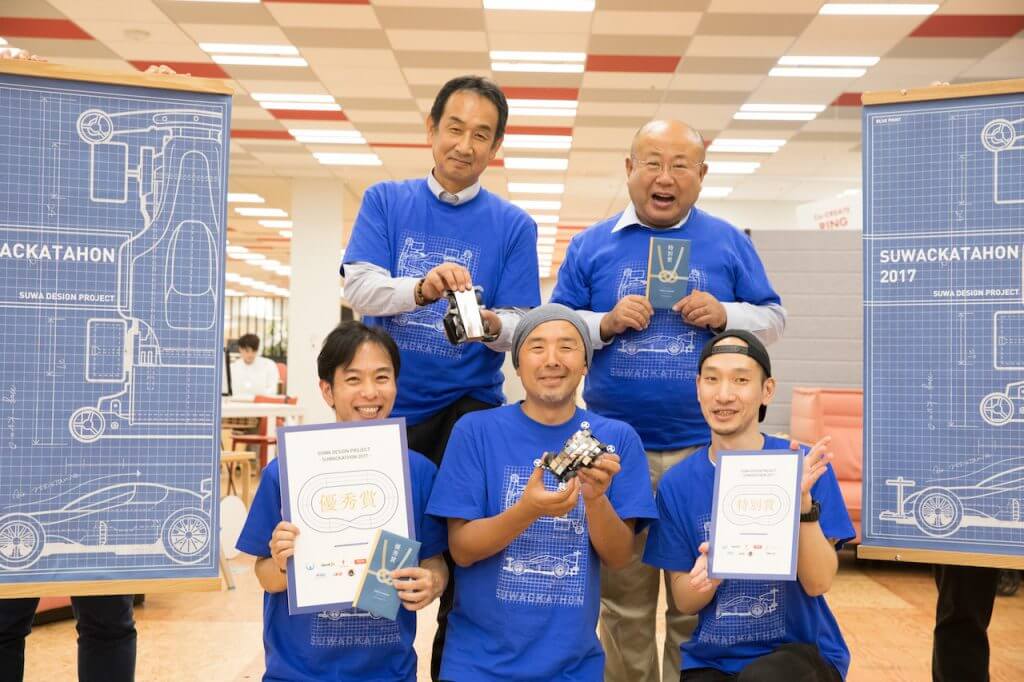
コンセプトメイキング
諏訪市での工場見学を経て、私たちのチームが興味を持った技術は株式会社松一の精密研磨技術でした。工場見学をした際に「月追揺杯」という、内側が精密研磨により磨かれていて、お酒を注ぐと内側がキラキラと乱反射する美しい杯が印象に残っていて、松一社と作ってみたいと考えたためです。チームでのワークでは、「輝き速そうに見える」をテーマに設定し、制作を進めることにしました。
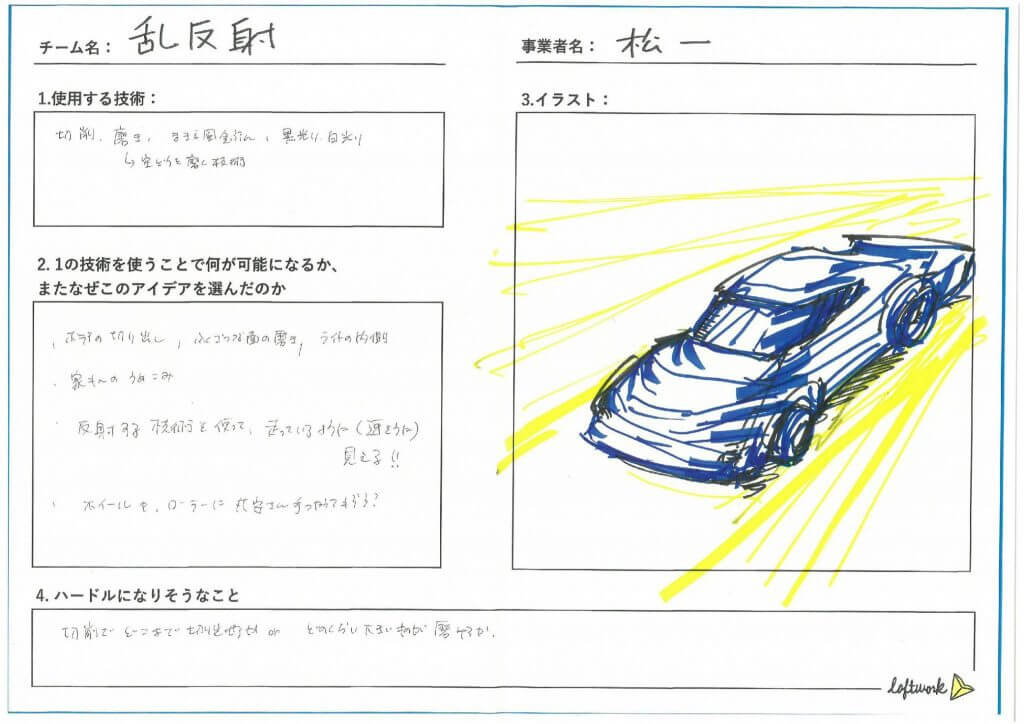
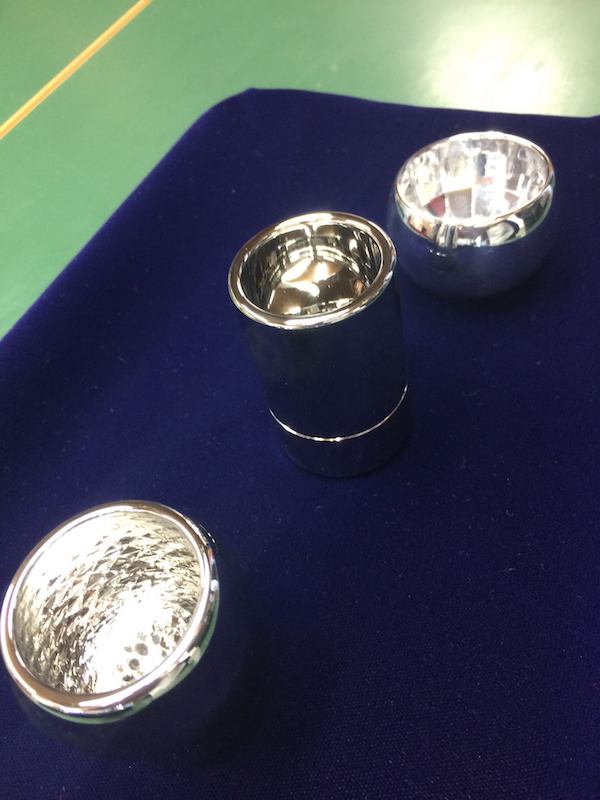
工場見学の帰りのバスの中で、「速そうに見える」とは?を考えながらそれぞれのイメージに合う画像を集め、集まった画像を整理してムードボードにしました。これを作ったおかげでチーム内、そして実際に加工していただく松澤社長と「何をしたいか」のイメージを早い段階で共有できたのではないかと思います。松澤社長に見ていただいた際に、甲冑の案を気に入っていただいたようだったので、鎧や刀のイメージを膨らませてみることにしました。
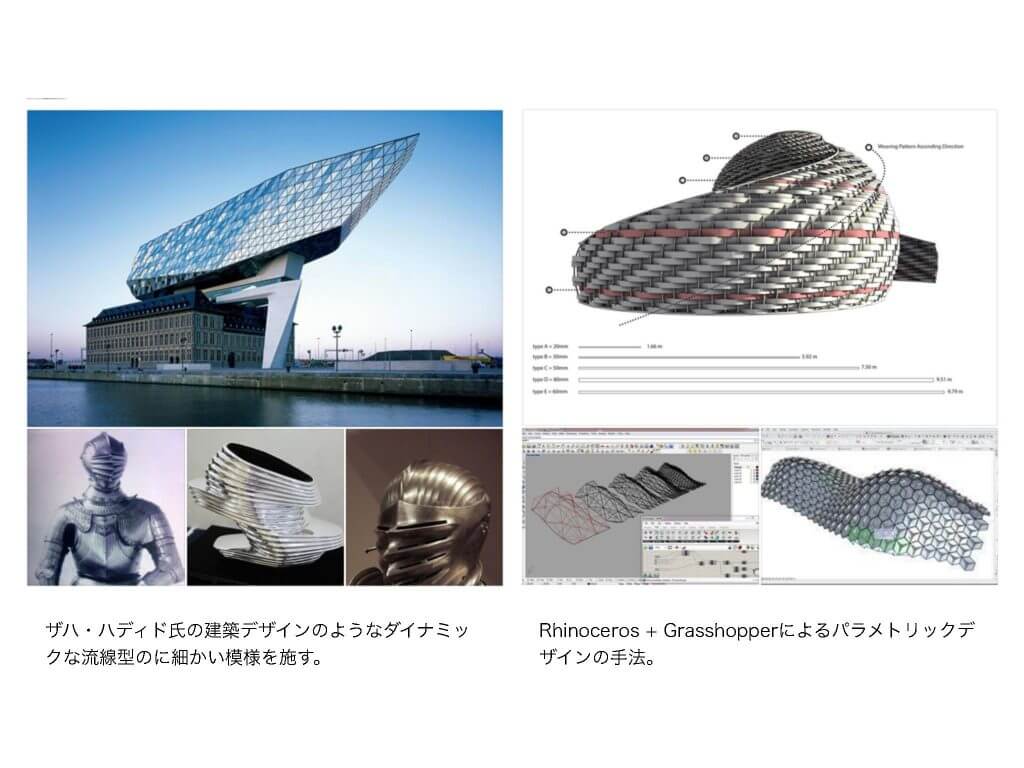
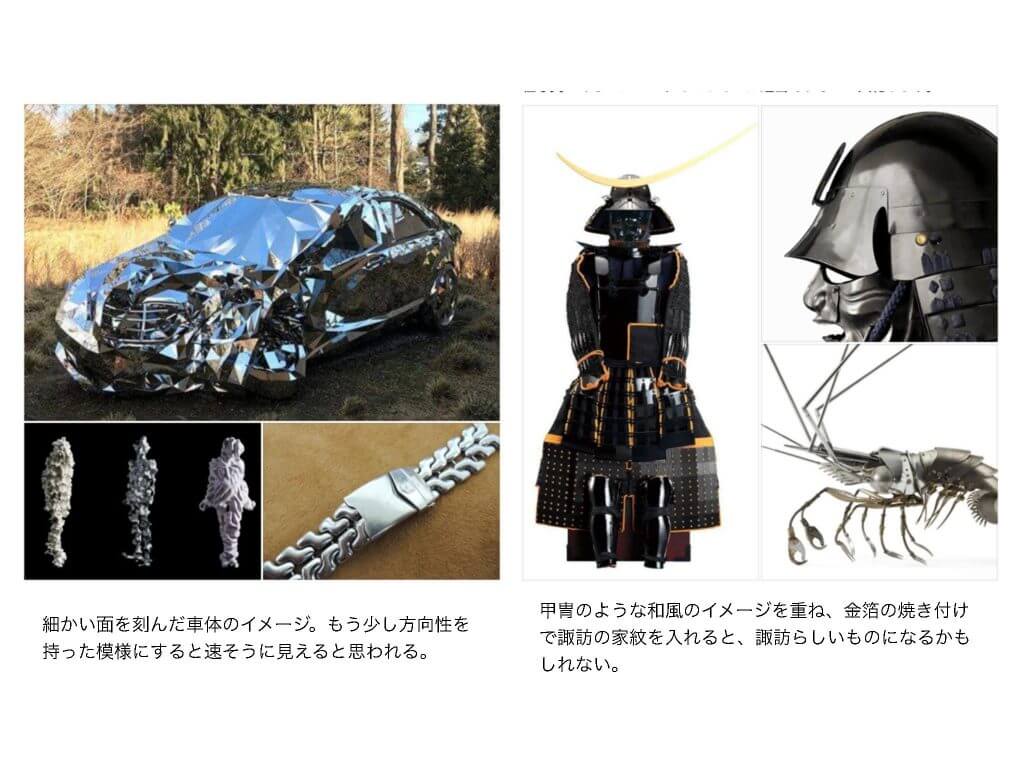
東京に戻って数日後に、チームメンバーで集まってスケッチしたスケッチの一部です。この時点ではそこまで完成形を意識していた訳ではないのですが、意外と完成したものはスケッチとズレていないかも、と後から振り返って思います。
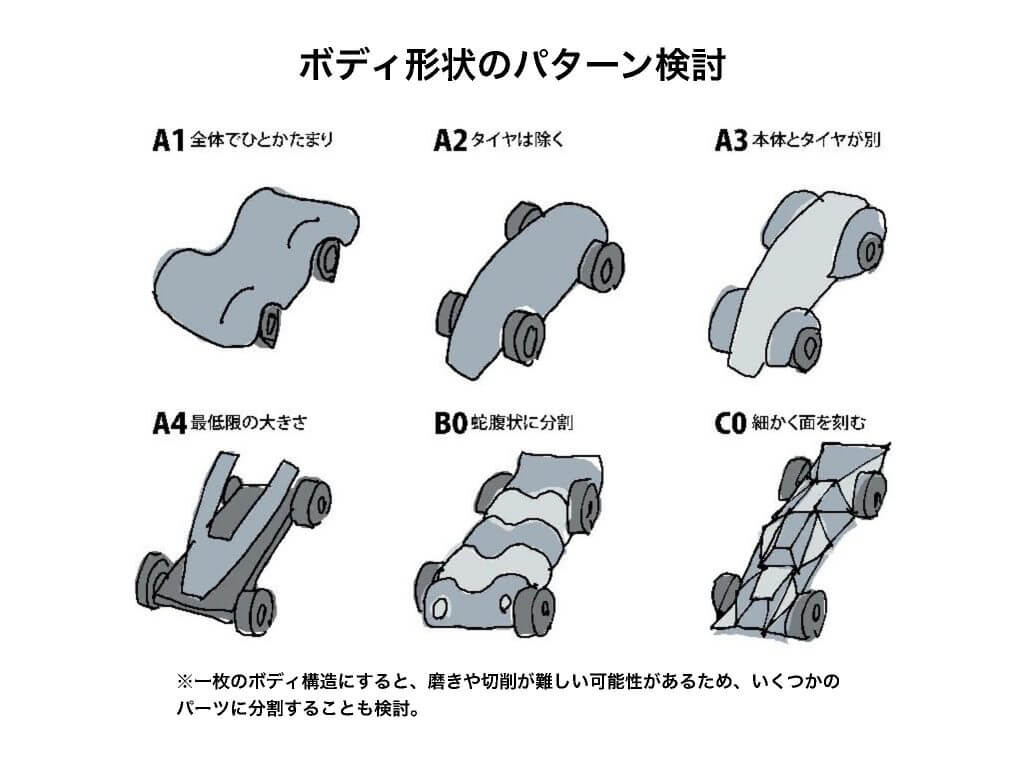
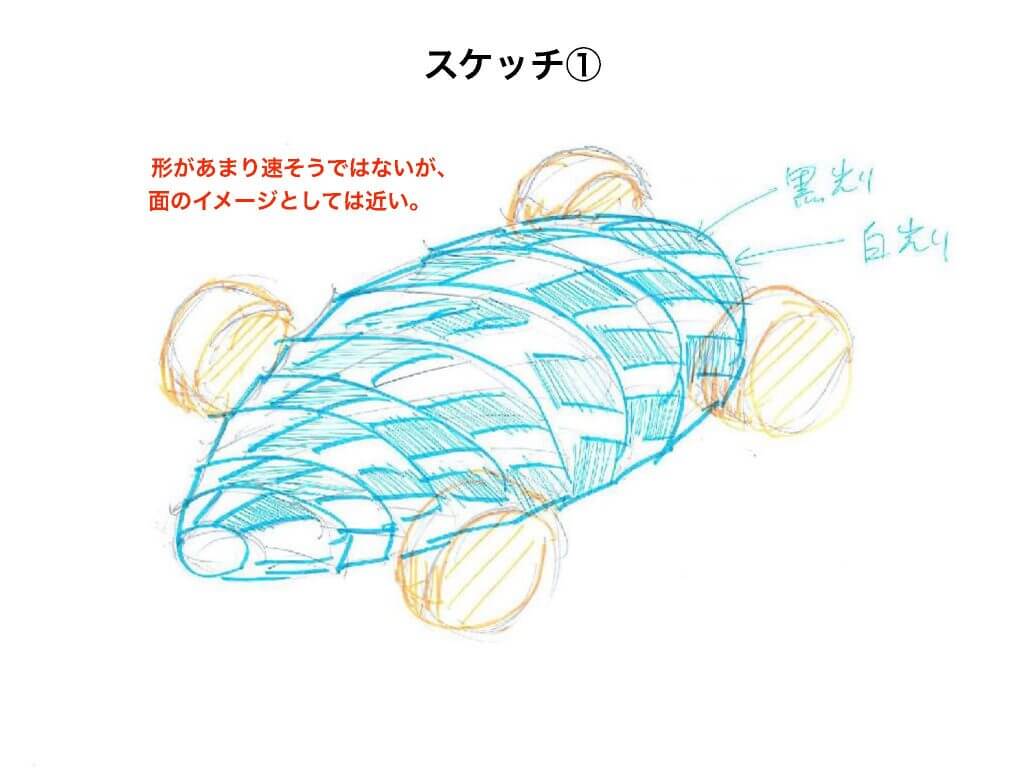
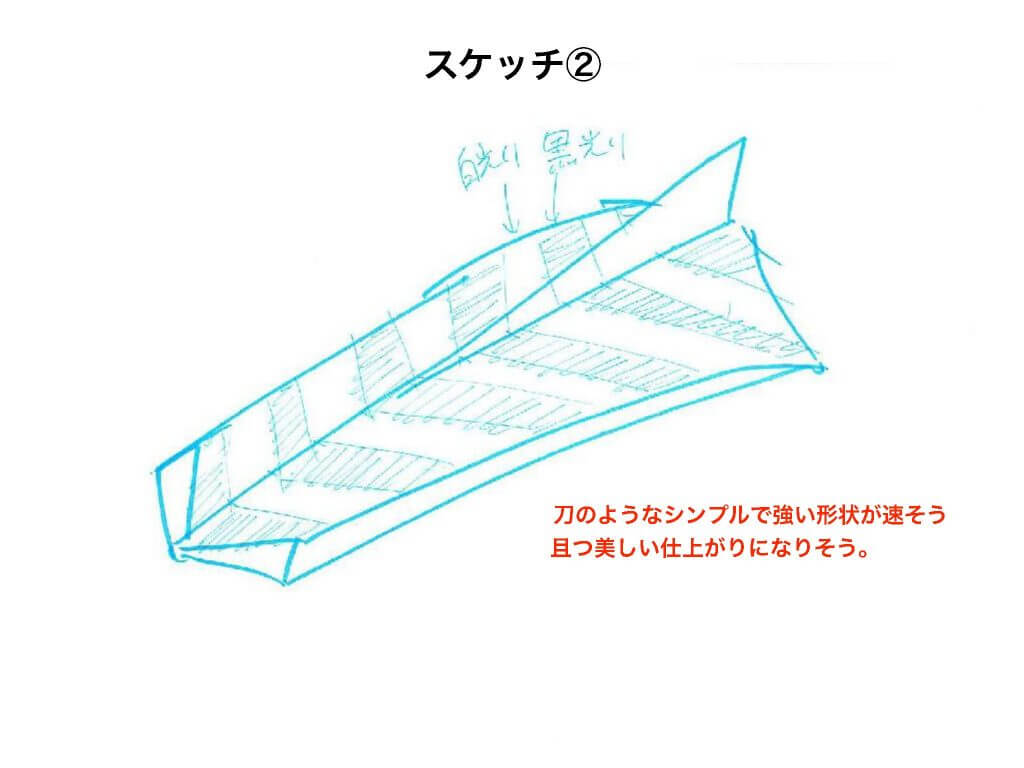
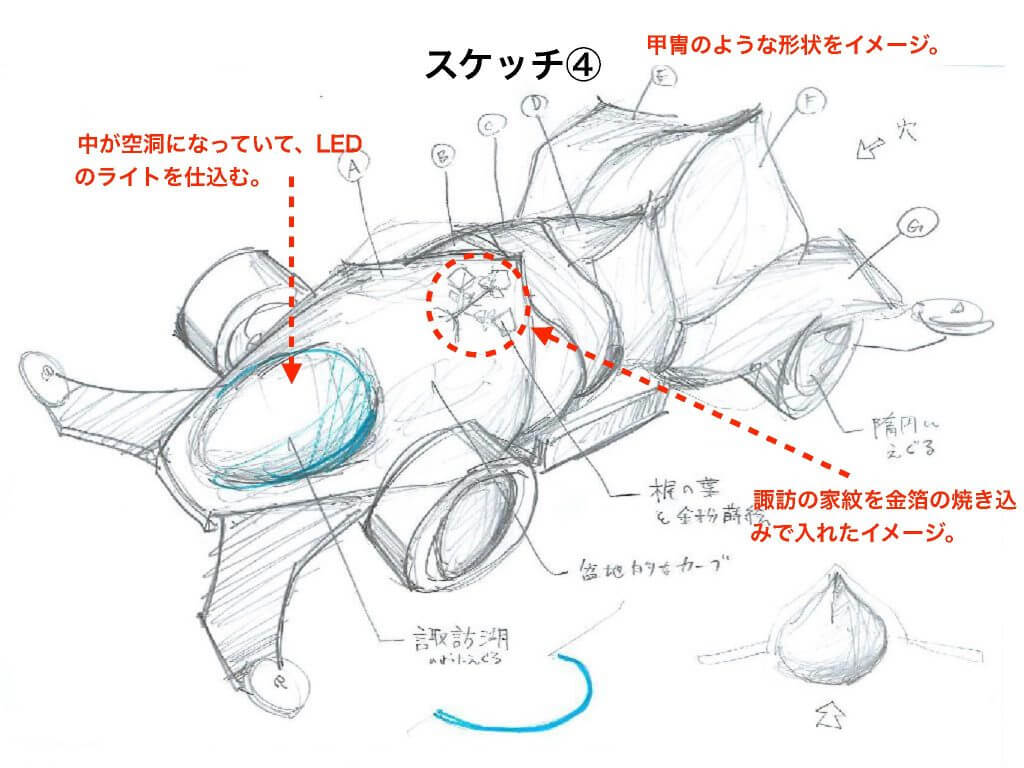
実はこのハッカソンに参加する前に、Fab Racers AcademyというFabCafeで行われた講座に参加させてもらっていて、そこでは自分の好きなモノからデザインのアイデアを考えてみる方法や車体のデザインやスケッチのコツなど、ミニ四駆をエンジニアリングやデザインの視点から、いろいろなことを学ぶことができました。
Fab Racers Academy
パラメトリックデザイン
今回のボディのデザインではRhinocerosという3次元CADソフトとそれをプログラムから操作するGrasshopperを使いました。この組み合わせは、有機的な造形の建築物をデザインする際によく使われるものです。プログラミングによる造形を行い、入力値を変えることで様々なパターンの結果を得て、その多くの結果からより自分のイメージに近い、あるいはより環境に適合する造形を選択することで、デザインを行うことができます。パラメータを触っている中で思いがけない形を見つけることがあったり、意図的にランダムな値を与えて想像もしなかった形が生まれることも。
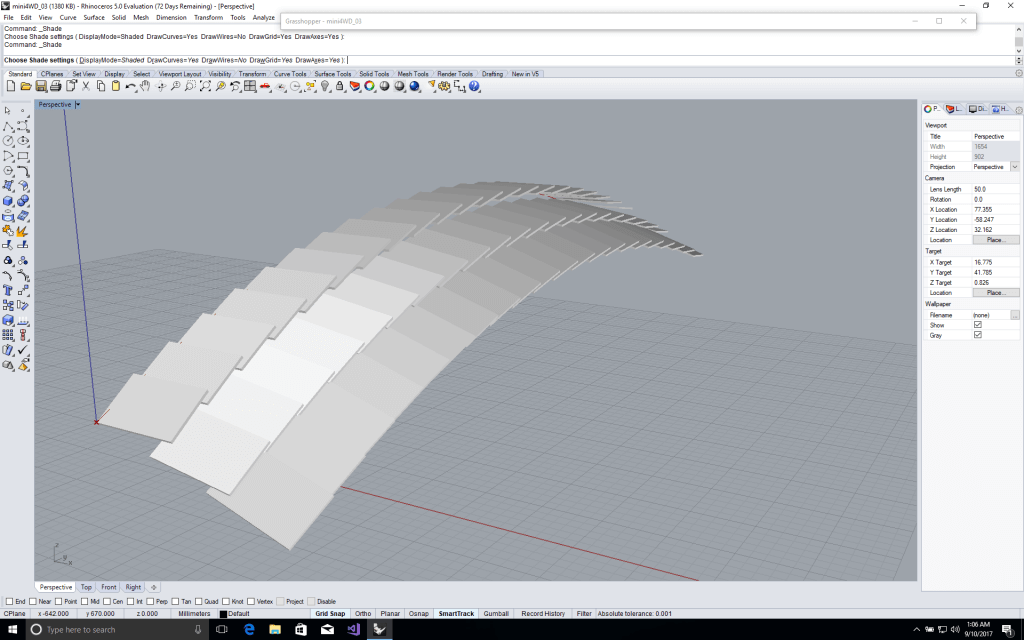
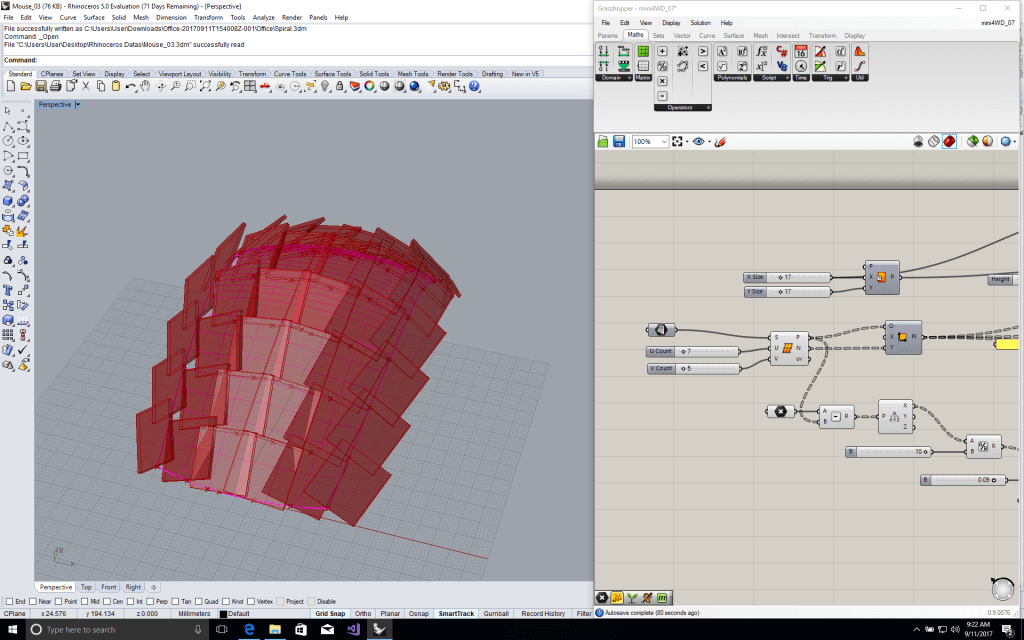
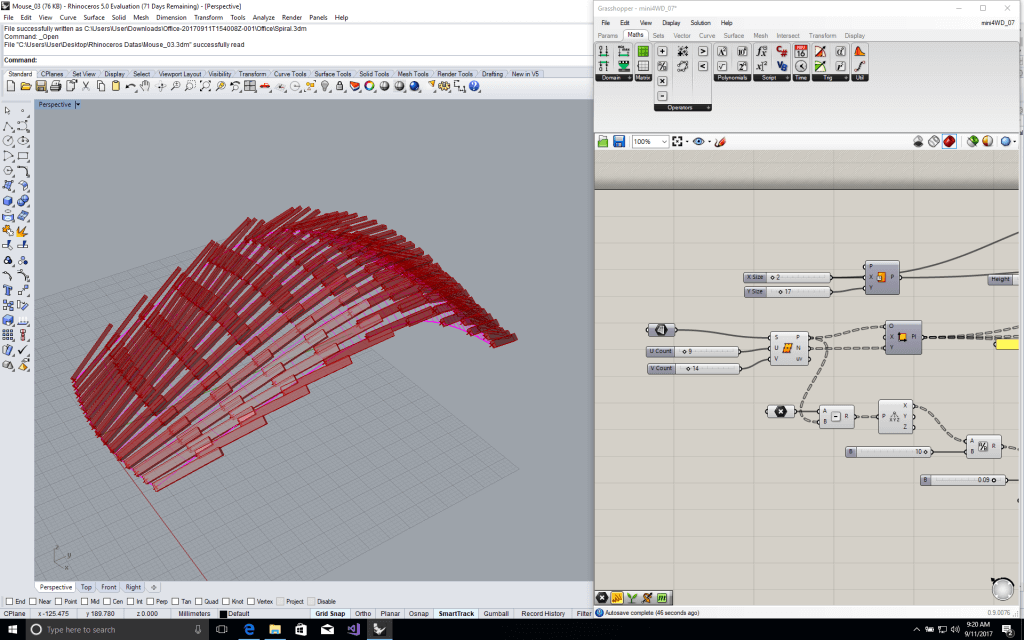
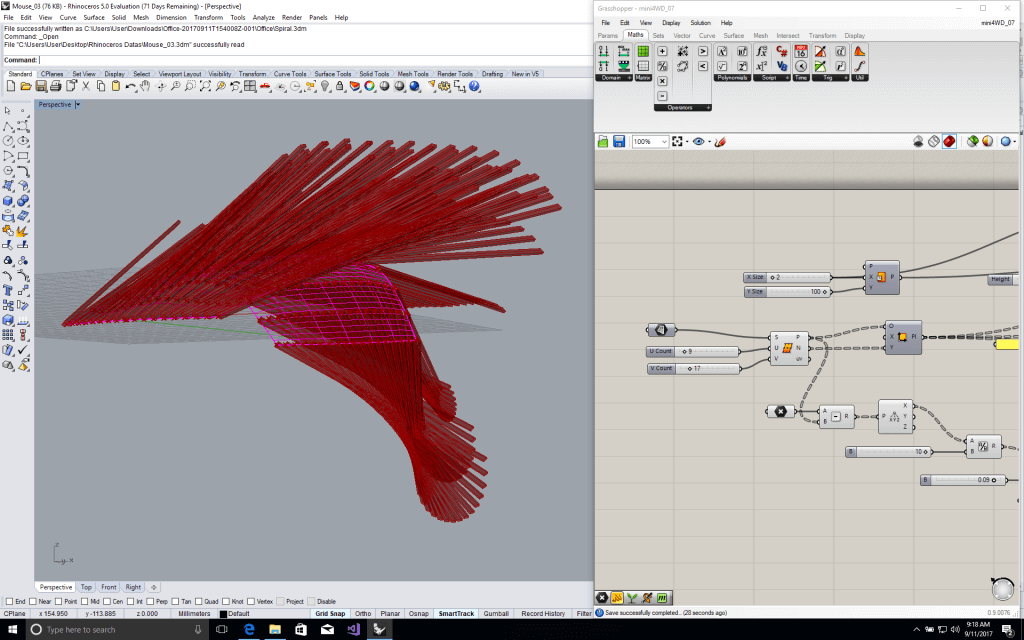
3次元CADを使うのも、Grasshopperを使うのもほぼ初めてだったので、教本のマウスの形を作るチュートリアルをやってみたり、その座標をGrasshopperから取得できるかテストしたりと、小さい検証を繰り返しながら進みました。ごくまれにプログラミングを失敗すると下の写真のようにおどろおどろしい形が生まれ…。
ぎゃあぁぁぁぁーーーーーーーーー!!!
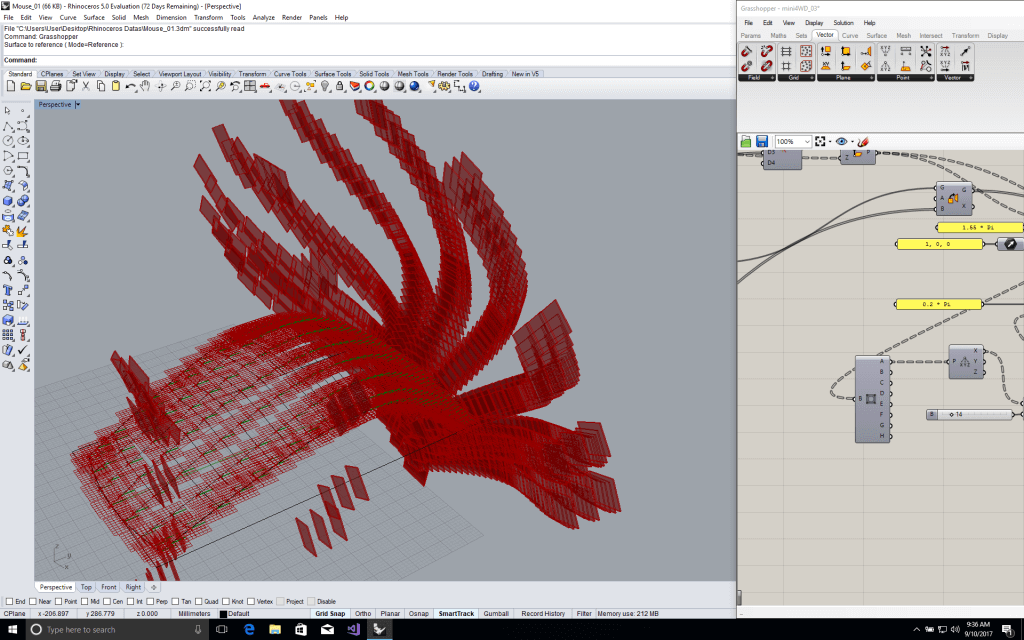
図形や波形、Webページを仕組み(システム)を使って生成しようとすると、どの部分を操作できるエンドポイントとして抜き出すかが問題になってきます。パラメトリックデザインでも、”パラメトリック”と言うだけあって、どの部分をパラメータとして割り当てるか、によって少しずつ違う顔を見せてくれます。私はこのエンドポイントをどう抜き出すかも含めて、デザインだと思っています。
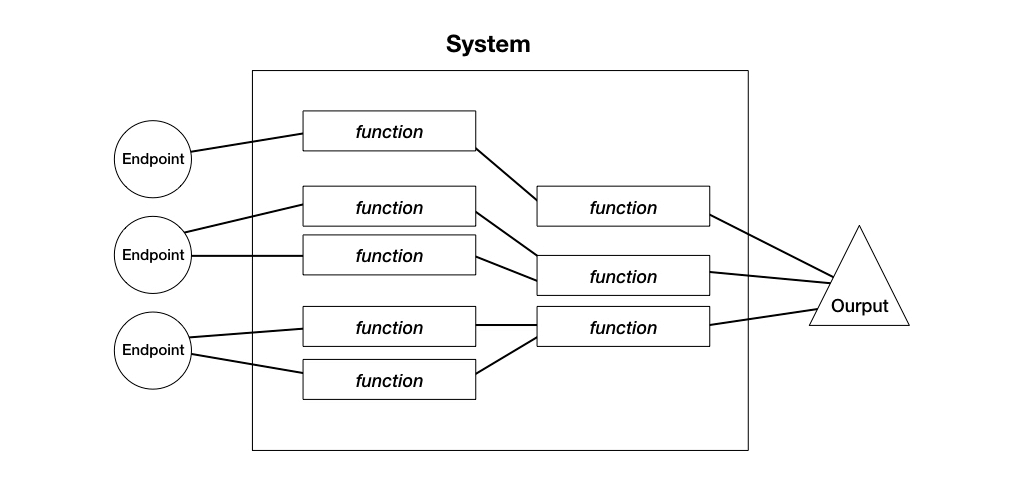
Rhinoceros+GrasshopperもFabCafeで行われた講座で入門させてもらったもので、Grasshopperの基本的な操作から、データ構造をうまくつかって形を作る話、ランダムな値を割り当てたサンプル群から、機械学習を使って自分の理想に近い形態に近づけていく講座など、スキルレベルに合わせて学べる講座です。
Grasshopper Essentials, May 2017
https://fabcafe.com/tokyo/events/grasshopper_may
私の好きなMax Billというデザイナーは「ひとつの仕組みからどのように形を展開できるか」を考えていました。コンピュータを使ったデザインは近年になって現れてきたように感じますが、根本的な思想は実は昔からあったんじゃないかとよく思います。産業革命に受胎した「デザイン」とコンピュータの時代を生きる私たち。それぞれを別のものとして考えずにひとつの線の上に乗せて、さらにその先を見て見たいと思う今日この頃です。デザインの巨匠達はコンピュータを使って何をするだろう?
画像元: https://www.stardust.com/max-bill-poster-variation-12.html
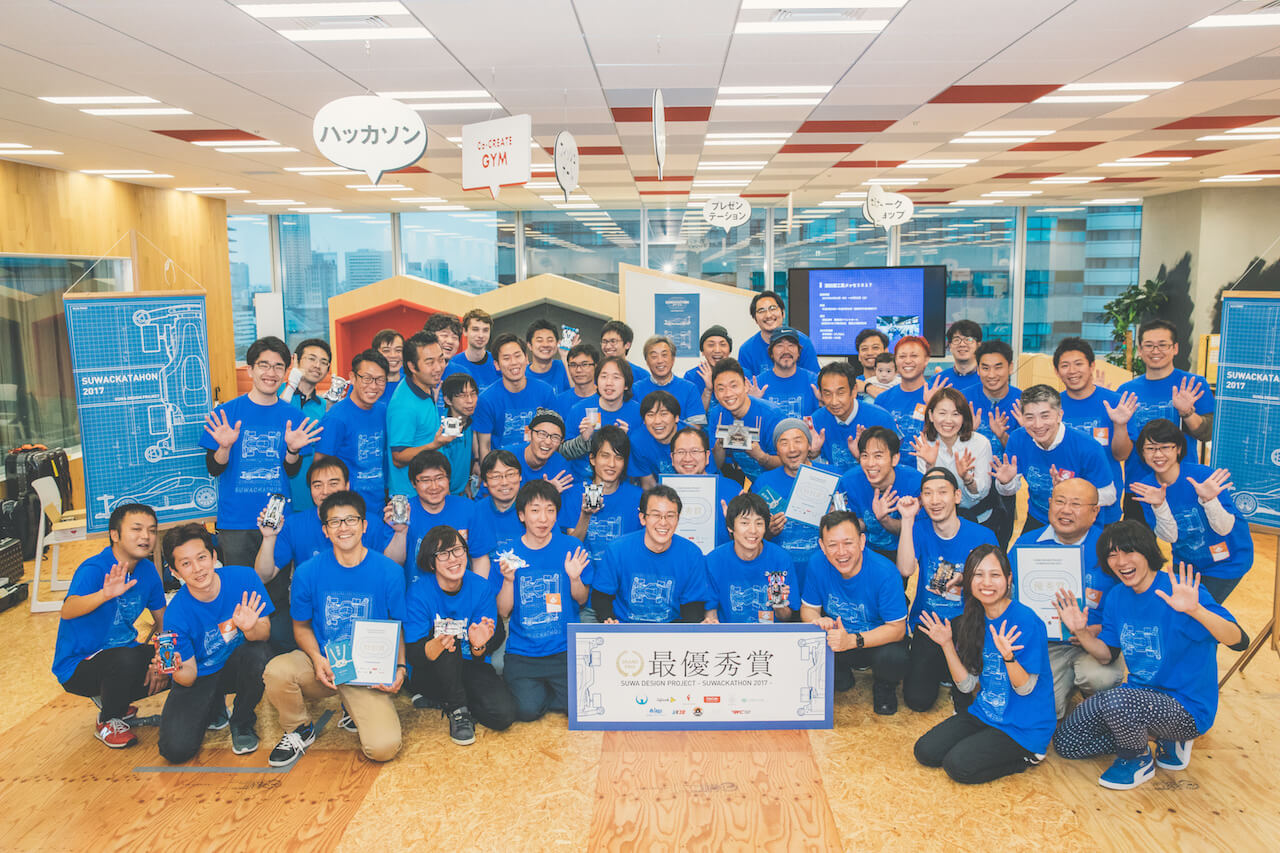
二つの壁
デザインをするところまで構想なので机上でなんとかなりましたが、物理的にものを作ろうとするとやはり難しいもの。実際に形に落としていく段階で2つの壁にぶつかりました。
その1:切削では作れない
当初私は「デザインを決めれば、あとは切削してもらって、磨いてもらって、OK!」とたかをくくっていました。ところが、松澤社長に相談していく中で、「そんな複雑な切削は時間がかかりすぎてこの期間では作れない」と言われ、甘い考えはもろくも崩れ去りました。だけどどうしてもギラギラのマシンを作りたい!と頭を何度も捻り、ひとつのアイデアを考えました。
小さなステンレス片をいくつも磨いてもらうことならできるかもしれない…。
下の画像がそのアイデアを松澤社長に説明したときの資料です。このとき、同じチームの佐藤と二つのデザイン案を進めており、僕がちょっと離席しているうちに佐藤が先に案の説明をはじめていて、話が既にまとまりそうだったので「もうこの案が表に出ることはないかもしれない…。」と半分諦めながら自分のプレゼンに挑んだのですが、説明を少ししたところで「それならすぐできるよ!」と快諾、2台作ることになりました。実はここが一番のハイライトで、心の中でガッツポーツ100ぐらいです。賞をもらえたことも嬉しかったのですが、技術面で工夫して難しいと言われていたことが実現できたことが嬉しかったのです。
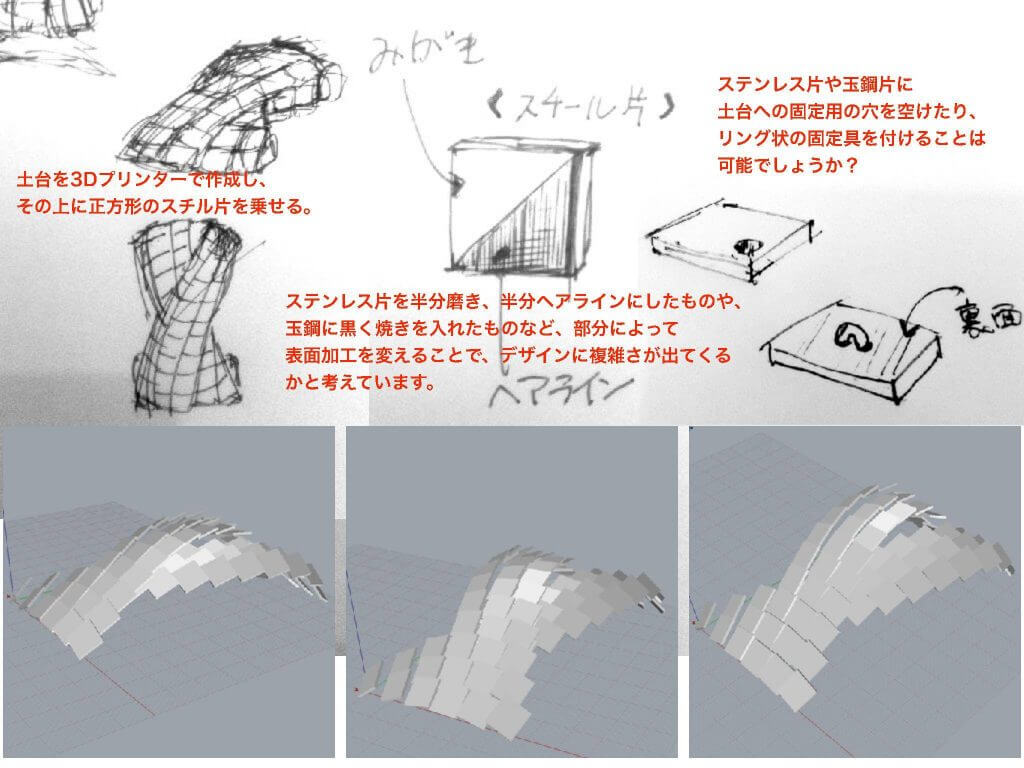
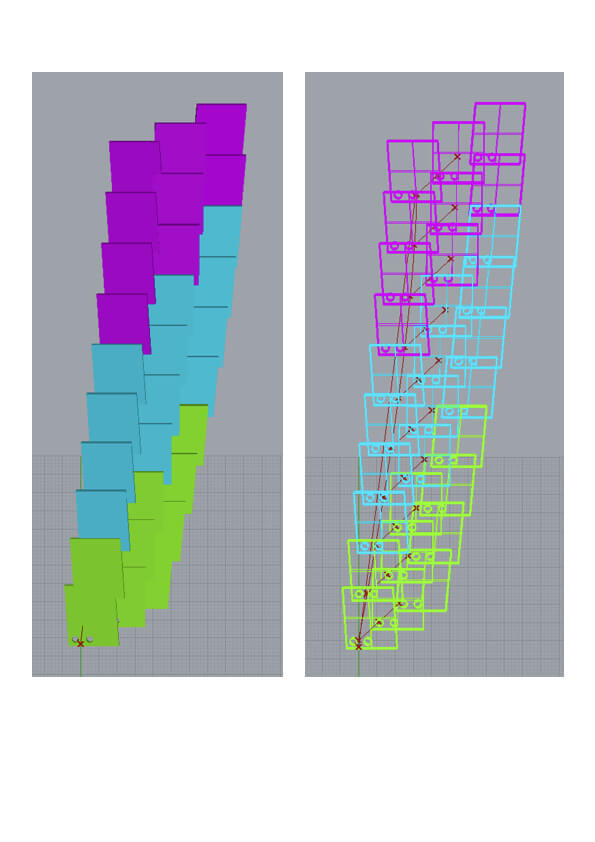
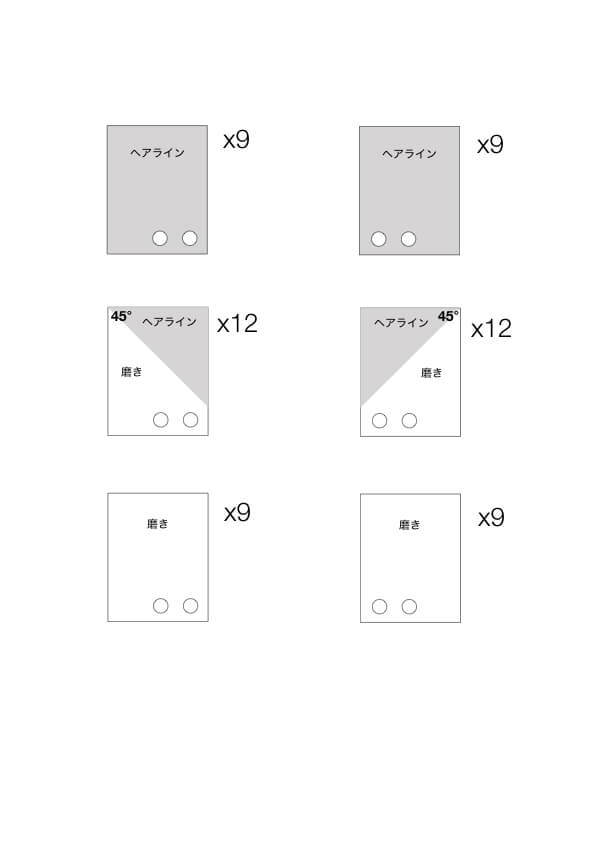
小さなユニットを組み合わせて作ることのメリットは大きく二つあります。
- 同じ形状のものを大量に作るので加工の手間が減る。
- 加工と設計を同時に進められるため、最終的な全体像の決定を遅らせることができる。
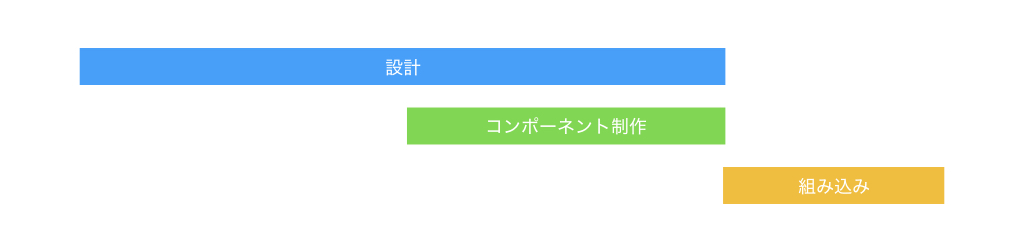
その2:3Dプリンタでは土台が間に合わない
これも私の考えが甘かったのですが、最後の全体像を設計しながら「全体設計が決まれば、あとは土台を3Dプリンターで出力するだけ!」と考えていました。いざプリンターを使おうと、FabCafeの川井さんに相談したところ、「こういう細かくて曲線的な造形はFabCafeにあるプリンターだと厳しい」とアドバイス、あえなく他の方法を検討することに….。とはいえこのときレースの一週間前、DMM.makeに出すにしてもトライしながら調整する時間はありません。形がパーツと合わなかったらアウト。そのときの最初の案が1枚目の画像。
他の案も川井さんやFabCafe)金岡さんに提案してもらったけれど…なんかちょっと僕が思うのと違う….。一晩頭を抱え…これなら….と出てきたのが2枚目の画像の案。レーザーカッターで作った板を貼り合わせて、橋のように土台を作りました。これならレーザーカッターで切り出すため、加工に時間がかからず、多少のトライ&エラーはできます。
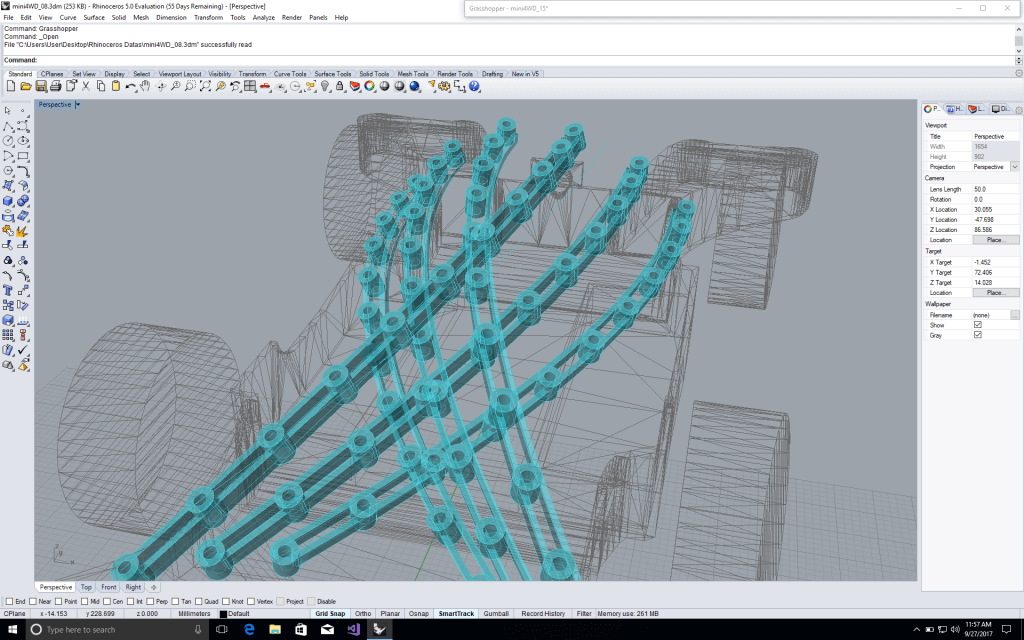
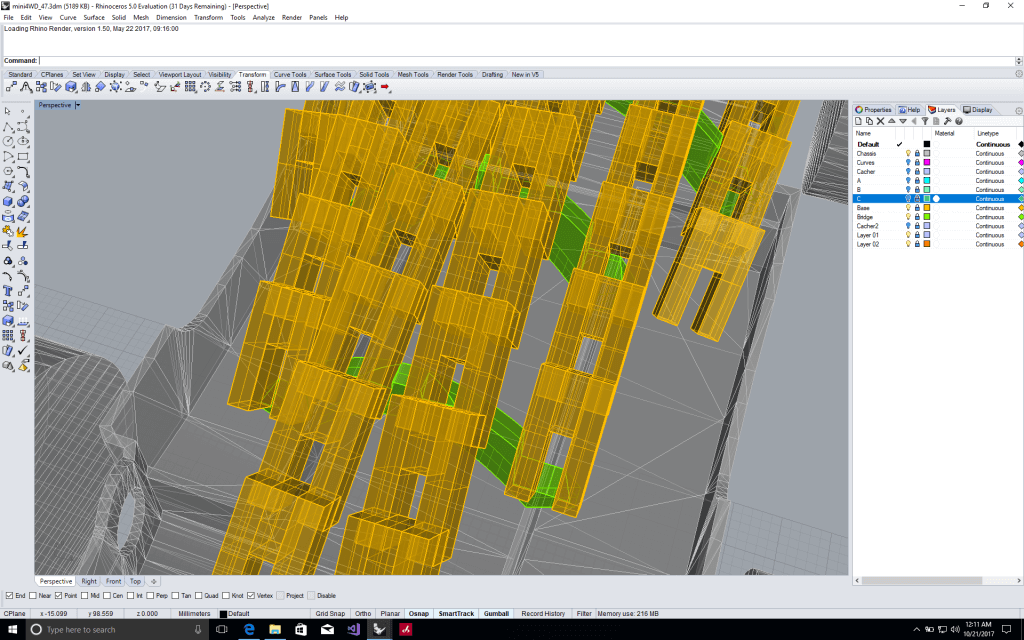
いざフィニッシュへ
なんとか土台も工面できたところで、最後の調整に入ります。左上は初期の設計ですが、クロスさせるとステンレス片の干渉が多く処理しきれないため、最終的なボディはもう少しシンプルな形にしています。また車高を低くしすぎると、シャーシとの干渉もあるため、少し上に膨らませるなどの調整を行いました。
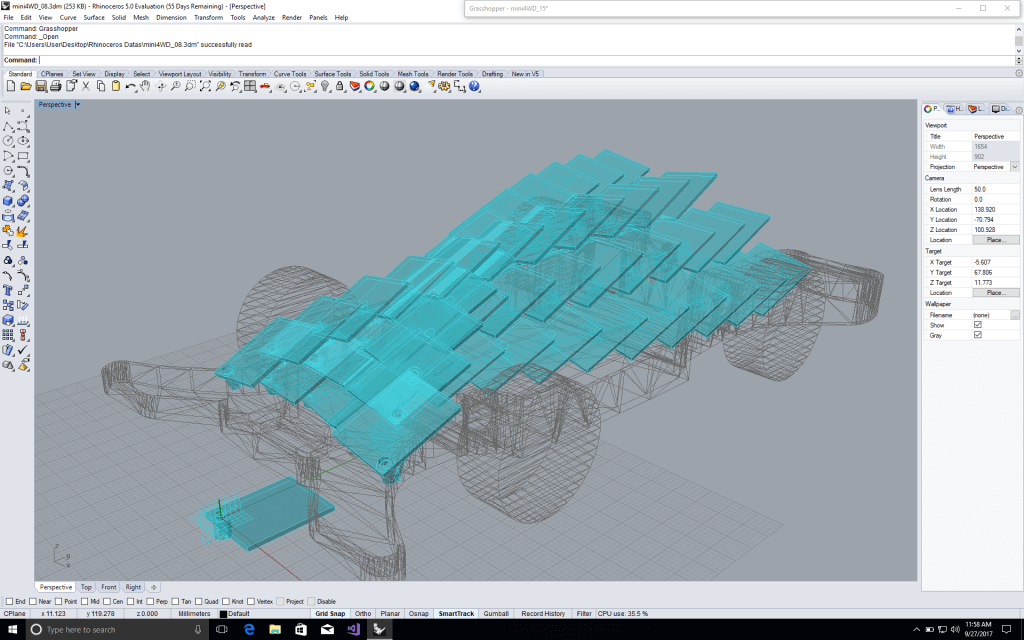
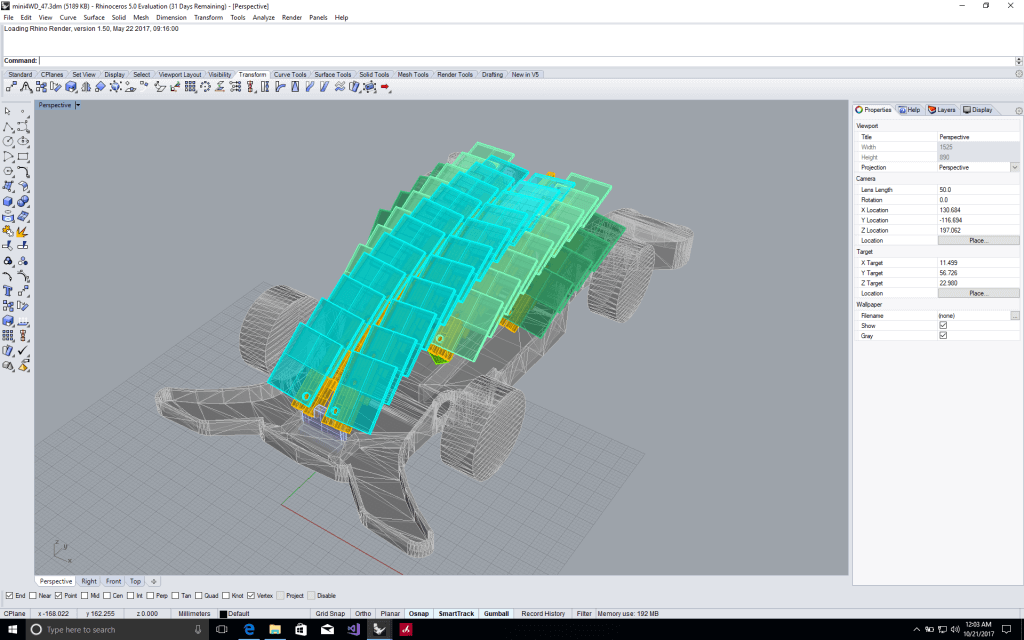
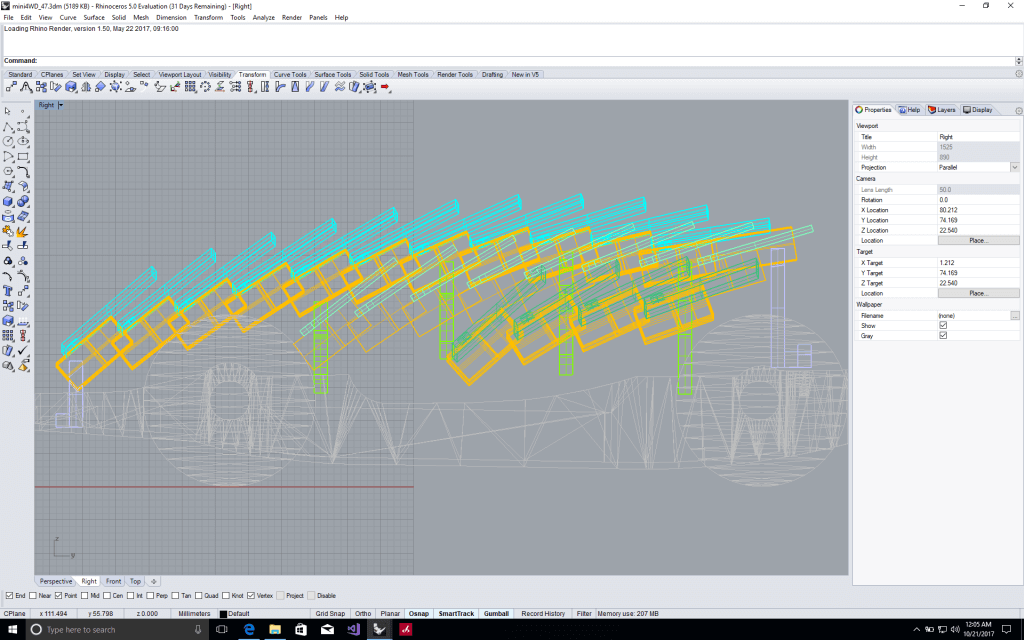
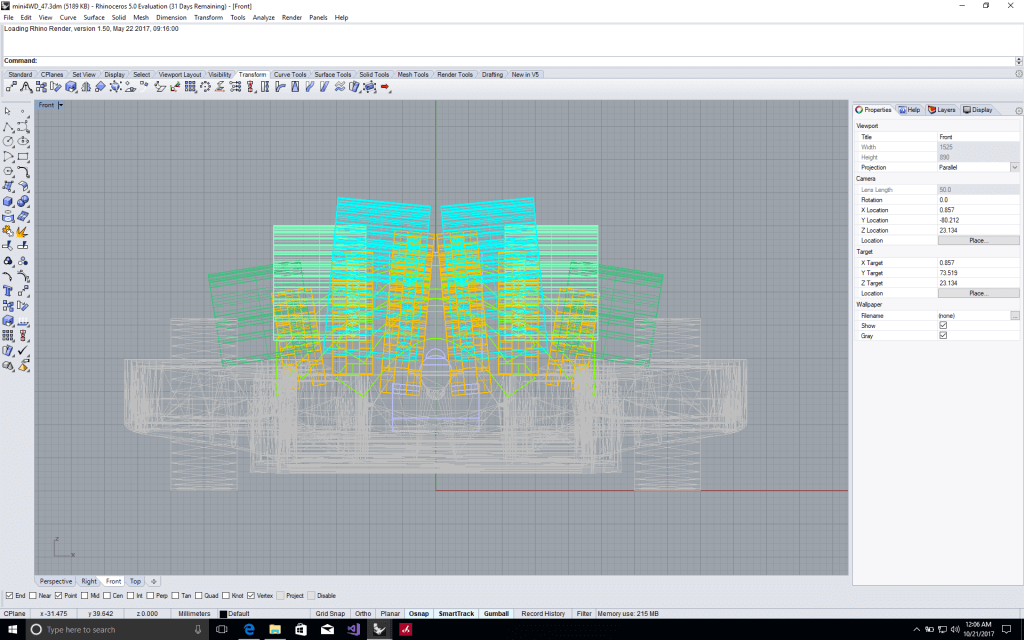
そして土台の組み立て。この土台、レーザーカッターで切った3枚のアクリルを貼り合わせていくのですが、レーザーカッターで切る時にサイズを間違えたり、貼り合わせがズレたりと、意外と大変。
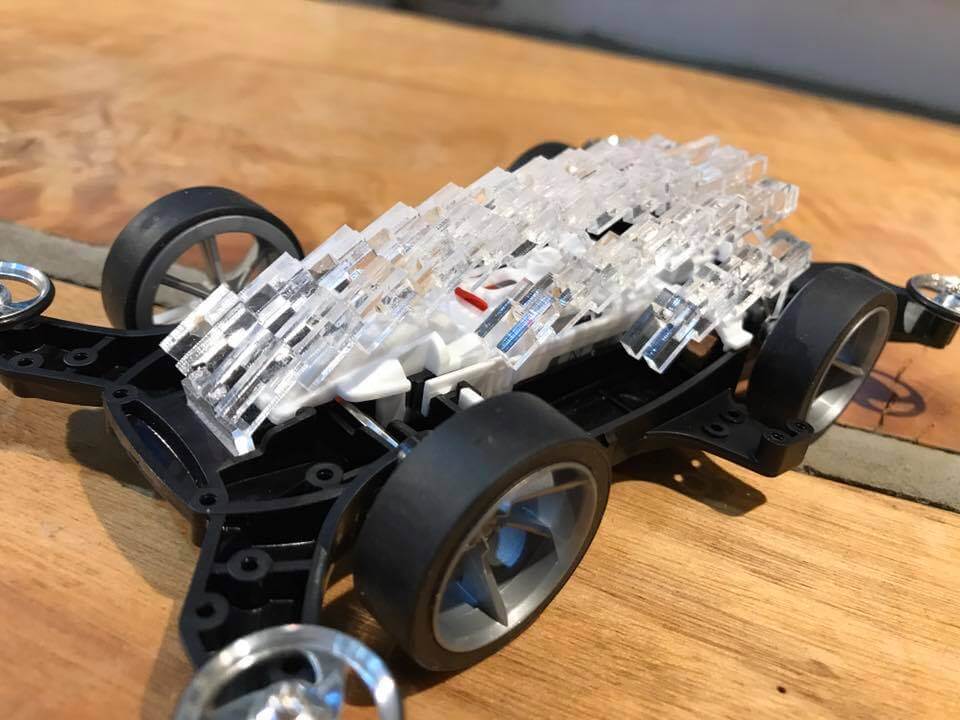
松澤社長から受け取ったパーツの組み込み。ひとつひとつネジで留めていくのですが、4時間〜5時間ぐらいかかり骨の折れる作業でした。
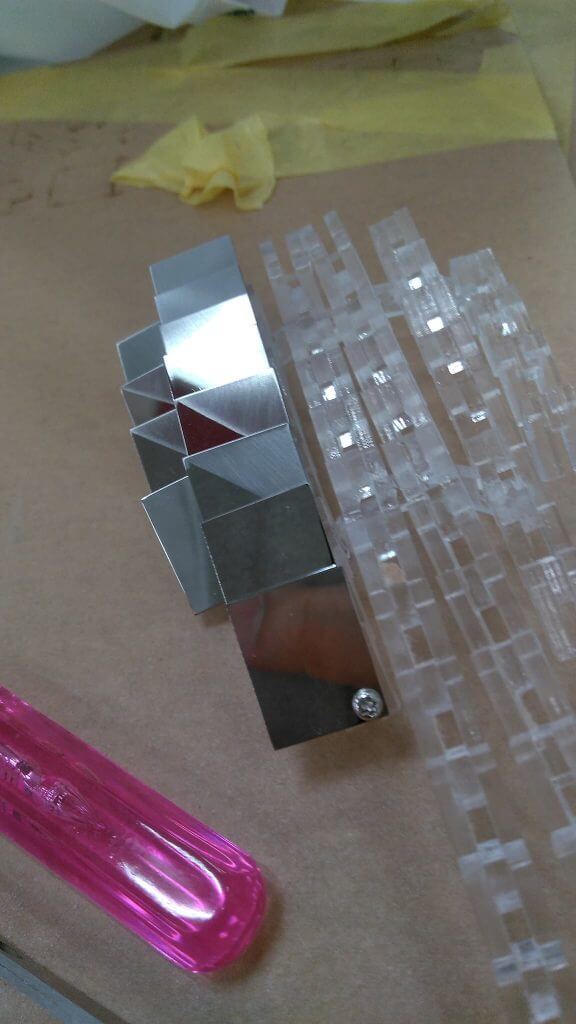
そして
ばぁーーーーーーーーーん!!
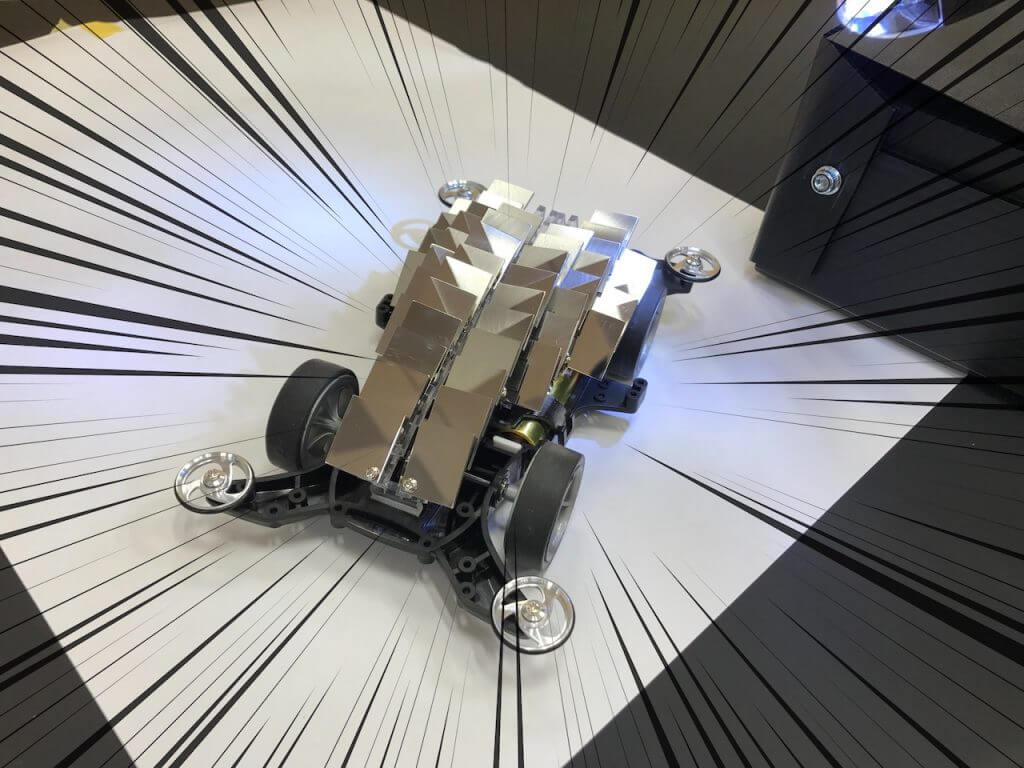
当日のレースの様子はこちらをご覧ください。
ミニ四駆を魔改造!世界レベルの精密技術でバトルさせると…
https://www.e-aidem.com/ch/jimocoro/entry/dango14
だれかの役に立つかもしれない気づき
その1:エンジニアリングを学ぶためのモチーフとしてのミニ四駆
ミニ四駆は子供のおもちゃとして作られたものではありますが、その小ささゆえにキチンと動いたりサイズが合うように設計していくことには骨が折れます。そういう意味では、今回の精密加工を得意とする諏訪市の工業との相性はバッチリ。その割に、小さいため材料などにかかるコストは抑えられます。なので、何か動くものを作ってみたい人は、いきなり大きなものから始めるよりは、まずはミニ四駆から始めてみるのもいいかもしれません。
その2:3次元CADスキルが開く世界
英語やプログラミングの授業が義務教育に取り入れられ始めていますが、次に来るのは3次元CADなのではないか?とちょっとまじめに考えています。これまで僕の中で、「Fab」という言葉で思い浮かぶのは、身の回りの小物をちょっと自分風にアレンジするようなものでした。ですが今回こうしてミニ四駆を作ってみて(ボディだけですが)、3次元CADを触りながら世界に手を突っ込んでいるような感覚を覚えました。3次元CADで造形したフィギュアがそのままプリントされることは当たり前なのですが、そうではなく誰かに加工してもらうものを設計し、組み立てたときに、ちゃんと画面と同じものが目の前に現れてきたときは、なんとも言えない不思議な感覚を覚えました。「あれ?なんでここにあるんだろう?」という感じです。そしてその後にくるのが、「あ!工場でしか作れないと思ってたものが自分でも作れるんだ!」という感動です。どこかの誰かに作ってもらうしかなかったものが、手の届くところにあるのが、なんだか嬉しかったのです(もちろんそのために協力してもらう人や工場は必要ですが)。自分が必要なものは(ある程度)自分で作るということが当たり前の世界になってきて、それができることとできないことの間に薄い壁が一枚ある気がしました。
まとめ
このハッカソンを通して、賞をいただけたことも嬉しかったのですが、TD(テクニカルディレクター)とクリエイティブの関わり方を模索する中、デザインの実現性として困難に直面したときに、技術的な工夫をすることでそれを乗り越えることができたことが、私の中で意味があったように思います。今後もすきをみてはいろいろ作っていこうと思います。
ということで、次回は何を作ろうかな?木工とかいいなぁと思っていたところに、ナイスな講座がOpenCUで開かれるようです!
MY CNC STOOL:自分だけのスツールづくり
木工の基礎を学ぶワークグループ:Shibuya WoodCraft Club Vol.2
Next Contents